One of the greatest complaints we hear from senior managers is “projects are successfully completed, but I’m not seeing a significant change to the bottom line.” That’s because in the Define stage of DMAIC (Define- Measure- Analyze- Improve- Control), Six Sigma experts don’t have enough information to quantify the benefits. They are predicting a bottom-line financial benefit without truly understanding how the process behaves, let alone how it would behave after the change. Without seeing the big picture, you may complete a successful Six Sigma project and see no impact in dollars for your organization.
There is a better way. With Process Modeling, you create a simple simulated model of the process. You will visually see which projects will affect the total output and which will sub-optimize the system.
Key advantages of integrating Six Sigma phases (DMAIC) with Process Modeling are provided below:
Overall interdependencies in processes
The standard Six Sigma toolbox has no way of showing the interdependencies between one area of the process and another. In complex change initiatives where there are interdependencies between processes, when incidents happen that cause delays, bottlenecks, variability etc., if you can’t show the interdependencies, understanding the system and resolving issues is very difficult. If you can’t understand the system and pinpoint the waste and bottlenecks, changing the system could be risky and typically does not provide the desired results. A simulated model shows those interdependencies, which allows you to uncover changes that will affect the overall system.
Risk-free experimentation
It is proven that real-time experiments are costly and can have an enormous negative impact on the system. If you are experimenting with a simulated model of the system, the only cost is setting up the experiment and reviewing the results. There are no negative impacts to system output or to the morale of the workforce in trying new process experiments. You can change the parameters, run various scenarios and, if the desired outcome is not achieved, you can pinpoint the root causes, all the while gathering more information about system behavior – without any disruption to the real system.
Reduced experimentation time
You can run hundreds of experiments a day rather than hundreds of days per experiment. Many processes have a cycle time of weeks or even months. Running enough replications of an experiment to validate the results can be overwhelming. With a simulated model, you can run as many computer simulations as you want and develop plans based upon the review of results.
Impact of change on the existing process
Processes that achieve the goal of Six Sigma (or a high sigma level) fall out of spec if the volumes change. For example, a 50 percent change to incoming calls to a call center may cripple a customer-oriented sales process. Planning for change in your system by using a simulated model to understand the effects of volume change, product stream substitution, staffing policy or other changes can significantly reduce project risks and the associated costs.
About the author:
Steven Bonacorsi is a senior master black belt instructor and coach. He has trained hundreds of master black belts, black belts, green belts, and project sponsors and executive leaders in Lean Six Sigma DMAIC and Design for Lean Six Sigma process improvement methodologies. Contact him at 603-401-7047 or sbonacorsi@comcast.net.
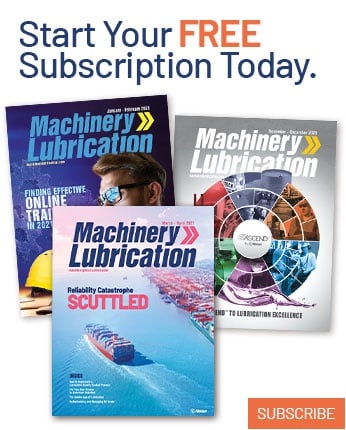