I spend a considerable amount of time in plants helping companies develop a strategic plan to improve lubrication practices. I've visited almost every type of plant and industry, from pharmaceuticals to mining, steel to food processing, and while the challenges may be different, one question is a constant: How should we lubricate electric motors?
For those who perhaps believe that there's really nothing exciting or controversial about lubrication, try initiating a discussion between a maintenance mechanic, an electrician and an operations manager about motor lubrication, then sit back and watch the sparks fly!
For the operations manager, it's all about preventing downtime. Nothing is likely to invoke more passion than an issue that has caused a recent production outage.
From my experience, too many plants adopt a "we do not grease motor bearings" policy, simply because of a previous lubrication-related failure. More often than not, such a failure was caused by too much grease being applied, causing grease to be forced past the seal into the windings of the motor.
Intent on preventing a reoccurrence, operations issues a decree that motors will no longer be greased, relying instead on vibration analysis to find an early sign of a motor bearing problem. That way, the bearing can (hopefully) be changed during a scheduled production outage.
Many companies who make this decision often switch to sealed bearings on all motors. Sealed bearings contain an elastomeric seal that prevents contaminants from entering the bearing and are not designed to be relubricated.
Useful in applications where harsh environmental conditions such as excess moisture or particulate contamination are present, sealed bearings typically fail when the lubricant - often a polyurea-based synthetic or highly refined mineral oil lubricant - fails due to heat and mechanical shear stress.
Useful in smaller motors, sealed bearings can have a much reduced service life in larger motors greater than 50 to 75 horsepower and can fail in as little as two to four years in some applications. Despite this, I have seen sealed bearings used in 300-horsepower and larger motors even though the motor is in a production-critical application.
I'm sure I will get several e-mails in response to this statement, but it is my belief that larger motors using open and shielded bearings can and should be lubricated, period. It defies logic to expect a bearing that is not periodically relubricated to last as long as one that is properly greased. Suggesting that better reliability can be obtained by not applying grease, in my opinion, is simply an excuse for poor overall maintenance practices and procedures.
So, how should electric motors be lubricated? Perhaps the most basic strategy is to apply lubrication engineering logic to calculate both the required regrease quantity and frequency.
While there are several different methods - some are based on frame size, others on actual bearing dimensions - methods provide a solid starting point for developing lubrication procedures. Similarly, using either a sonic or ultrasonic device to assist in "hearing" when the bearing is adequately lubricated can provide an added degree of precision and a truly optimized relubrication strategy.
Even among companies that do lubricate motor bearings, a common practice is to assign this task to electricians. The logic is that the electrical department is responsible for delivering electric motor reliability, so any motor-related maintenance task, including regreasing, should rest squarely on its shoulders.
While there's no reason why this can't work, in my experience, when electricians are instructed to lubricate motor bearings, a lack of familiarity with mechanical systems and mechanical system maintenance often leads to a decision to "do nothing" (not grease bearings) for fear of inducing more failures than they solve.
Again, this is just my opinion, but I firmly believe that regreasing motor bearings is no different than any other bearing and should be the domain of the mechanical maintenance team, not electricians.
The only time when a regreasable motor bearing should not be lubricated is if it has not been greased for two to three years or more. Under these circumstances, exercise caution since old, hardened grease can prevent even distribution of new grease throughout the bearing, perhaps leading to the new grease being forced through a seal or damaging a bearing shield. Other than that, it's pretty much a given that a bearing that is relubricated will last longer than a bearing that is left untouched.
So, avoid motor bearing failures and the related downtime. With very few exceptions, bearings last longer when they are properly lubricated.
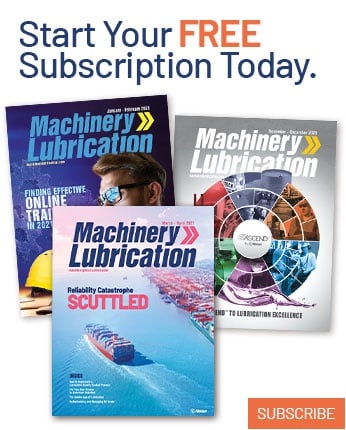