Many are aware of the use of motor circuit analysis and infrared imaging in a predictive maintenance (PdM) program for motors. It is a program that, when performed properly, increases uptime, reliability and productivity, ultimately impacting the thing most managers want to see: lowered or stabilized maintenance costs. However, there may not be an understanding or awareness of the benefits and impact that an effective motor management system can have on that cost.
This article will show basic key elements for a motor management system and provide an understanding of why a motor management system is much more than just a reliability and testing program. In fact, motor reliability and testing are two key components that make a significant contribution to a motor management system.
Infrared thermography is just one part of an effective motor management system.
SHORT STORY
There was once an employee who asked a lot of questions. This caused much consternation among the bosses and fellow workers. "A-ha!" the bosses thought. "We will promote him. Then he can answer his own questions!" They continued on, happily thinking this was the answer; however, to their chagrin, more questions followed.
In the meantime, this newly promoted supervisor was given approximately nine hats to wear. One of them was to oversee the Motor Shop. So, where else could he start? With a bit of authority that accompanied the promotion, he created a team. A few questions got answered, a few things changed. Before anyone knew it, a motor management system began to take shape.
The first six months were very difficult indeed, and another 12 rough months would pass. After 18 months, a faint glimmer of light could be seen at the end of the tunnel. Though people had fought tooth and nail against it, a few eyes began to flutter and some popped open when it was revealed that repair, inventory and purchase costs had been reduced nearly $1 million. Suddenly, the questions, ideas and actions no longer seemed so trivial.
Looking back, it was easy to see the well-traveled road littered with the debris of good intentions, false assumptions, erroneous information, etc. All this and more created a climate where bad decisions were made and money wasted.
As an example, the first practice stopped in those first 18 months was repairing motors for $900 that only cost $200 when new. This was just the tip of the iceberg. Energy-consumption issues were later added to the equation, as well as other reliability principles and testing.
WHAT IS IT?
Managing motor assets requires that a motor's location, function, repair, testing and reliability history be documented, preferably in one place. This documentation should be easily accessed for research and used to assist in making correct and appropriate repair/replace decisions. Motor testing doesn't create a motor management system, but it should be a key component. At a minimum, such a system should have the following components:
-
A motor manager: someone who is in charge and accountable
-
Storage: outdoors is not acceptable
-
A preferred, accountable repair facility
-
Repair specifications for the repair facility to use
-
A cost-saving contract for purchasing new motors from a primary vendor
-
Reliability testing: off-line, on-line, infrared and even vibration
-
Acceptance testing of repaired motors and new motors, if possible
-
Tracking motors from purchase through scrap and the history in between
-
A decision tree for determining repair vs. replacement
-
A system to address energy consumption and efficiency
WHO'S IN CHARGE?
The person in charge (the motor manager) doesn't have to be a motor expert; however, he or she should be somewhat knowledgeable on motor basics. This person also needs to have knowledge of the motor contract with the preferred new motor vendor and the preferred motor repair facility. The motor manager oversees all aspects of motor purchases, repairs, modifications, history and disposal. He or she should be a member of the site equipment reliability team and should interface often with the reliability manager on matters pertaining to motor testing and reliability. Managing motors doesn't have to be this person's only area of responsibility. He or she can wear other hats, as well.
Once an effective motor management system has been in operation for a time, and employees and other managers become educated as to how it works, it should become easier to manage.
STORAGE
Motors never should be stored outdoors. Ideally, they should be stored in a climate-controlled facility. Climate-controlled storage facilities are rare.
Warehouse personnel are normally tasked with the day-to-day activities of normal motor storage - from receiving, issuing to and shipping to the repair shop. Personnel should be familiar with how to handle and store motors to avoid incidental damage during the storage process.
Large AC motors (high voltage) sometimes need special handling and storage areas. Connect motors with internal heaters to a voltage source while in storage to keep the windings dry.
REPAIRS
Every effort should be made to identify a preferred and accountable motor repair facility within a reasonable driving distance. Preferred means a vendor that can handle just about everything that you send to it. This facility shouldn't object to inspection visits and should warranty its work in some manner and work with you on all levels of repair. Repair quality and reliability should be the guiding criteria.
A contract with a preferred repair facility can be negotiated to reduce repair cost over what it may have been. An ideal situation would be that the repair facility is also a dealer for the preferred new motor vendor.
Then there are the special, one-of-a-kind and non-standard motors that have to be addressed. Have you seen the suffix TY, TCY, TZ or TCZ (for instance, 286TCZ)? If so, they are the "non-standard" variety and might only be acquired from an original equipment manufacturer (OEM), not the motor manufacturer.
If the OEM is totally out of business (not acquired by another company), a replacement motor may not be available. Having the right repair facility can come in handy with these motors. Also, by having an understanding of what alternatives are available and the knowledge of what to use as a substitute, the plant can stay running.
NEW MOTORS
Anyone operating without a preferred new motor vendor contract could be losing money. A contract with a preferred new motor vendor may reduce purchase prices by 20 to 40 percent. Large corporations may already have a contract with a preferred new motor vendor. This should be followed, whenever possible, within the guidelines.
RELIABILITY
Reliability consists of many things, such as engineering, testing and inspection:
-
Engineering: Is the motor designed and/or repaired to perform the task it is asked to do?
-
Testing: motors and their circuits.
-
Infrared: It is very important to have baseline images and stated "normal" temperatures.
-
Vibration: baseline data.
When testing or inspecting a motor, it is important to ask, "Is this the motor I think it is?" or "Was this the same one that was there the last time?"
A motor reliability and testing technician shouldn't be considered the motor manager. However, the tech is a key partner in the management of motor assets, along with maintenance managers, mechanics, warehouse people, purchasing people, etc.
The reliability and testing technician also should have a working relationship with the preferred repair vendor in order to assist in problem resolutions.
DECISION TREE
Every motor management system should have a decision tree. Use the tree to help you make repair or replace decisions.
Most decision trees lack one important item. This is a branch or section to help determine whether a motor should be equipped with a roller bearing on the shaft end. This is a critical decision for motors driving equipment through belts. Don't construe this to mean that all motors driving belts should have a roller bearing on the shaft end. Each case should be considered separately as to whether a roller bearing would be applicable. This issue is also very important when making a purchase decision for a new motor.
TRACKING
Tracking a motor from birth to burial is difficult, at best. A properly functioning and effective motor management system makes it easier and can pay for itself in man-hours saved, energy efficiency, reduced inventory and (above all) reliability. A key element to tracking is assigning a unique identification to each motor. The ID should not be removable. A good practice is to engrave the unique identifier on a motor. Engravings aren't easily removed and remain legible for years of service. More often than not, they outlast the motor.
The area where the J-box is mounted normally provides a large enough surface area, as do other areas on the motor. Don't engrave end bells with the identifier in the event an end bell is replaced. The engraving should be as deep as possible and legible. Stamping is not recommended because there is a risk of cracking the casting.
Relying on the nameplate for identification can be frustrating, especially if the nameplate is removed or becomes unreadable because of corrosion, etc. Motor shops often install a replacement nameplate, but only the basic information is usually put on it and other important information may be lost if not recorded elsewhere.
There are a number of ways to set up an identifier, but it should be uniform and not change from year to year. For example, a numeral system based on the year and the sequence the motor arrived can be assigned along with a letter designation for the name of the site - for instance, 99-035V. The 99 means it was 1999. The 035 means it was the 35th motor identified in 1999. The V stands for the name of the plant site. If it was an older motor that had not yet been identified, it would be assigned the next sequential number.
HISTORY
History is a sequential documentary of the life (birth to burial) of a motor. It's a very important piece to help determine whether to repair or replace a motor. Normally, a motor stator can't withstand many burnouts and rewinds without the core becoming degraded. Without a history, it's very difficult to know how many times it has been rewound, much less what else has been done to it or where it has been.
History can be kept in many forms (a sample is shown below) and is normally tailored to a particular site or company. Whatever form it takes, it has to be easily used and not fragmented in different places to get a complete picture.
A number of motor testing systems allow for history entry and retention. However, they present some limitations in regard to documenting a complete birth-to-death history, especially if there is no formal motor management system in place. History then becomes fragmented and sometimes of little use unless diligently administered. History is the lifeblood of any motor management system.
HISTORY SAMPLE |
ID: 99-035V Shop #172986 50-1780-326TPH S/N: none US Electric 460v 65 FLA 90-eff 82-pf 56 Bars 48 Slots Note: Open style, vertical mount, shaft down, oil bath top bearing 02/15/1999 - New motor: PO 14598V: Acceptance ck good: Test Run OK 02/20/1999 - Installed: 40628971P: #1 River water pump: w/o V179263 10/31/2003 - Removed: 40628971P: Grinding noise: No oil: w/o V613578 11/15/2003 - From Repair: Acceptance ck good: Reconditioned 05/16/2004 - Installed: 40628972P: #2 River water pump: w/o V798642 Note that ... Reconditioned = Bearings, machining, cleaning, painting, etc. Overhauled = Rewound along with reconditioned items. |
EFFICIENCY
In this day of increasing energy costs, particularly electricity, it pays to be energy conscious.
According to the U.S. Department of Energy, electric motors consume a large percentage of electricity used in American industry. On average, approximately 63 percent of industrial electricity is consumed by electric motors. This percentage can reach 75 percent or more in certain industries. Also, motors can consume five to 12 times their initial purchase cost in energy per year. If you consider that a 25-horsepower motor, running 24/7, can consume up to $15,000 in energy per year and a 100-horsepower motor can consume up to $56,000 in energy per year, even small reductions in energy consumption per motor could result in substantial savings. Additionally, in the case of motors up to approximately 50 horsepower, the savings difference between using a standard-efficient vs. a premium-efficient motor could pay for the premium motor in one year. Every year after that would be money in the pocket.
Repair practices and quality can significantly influence energy consumption over original design. A rewound motor, especially if it was poorly done, can significantly increase energy consumption compared to the original "as built" specifications. That's a very important item to consider when making repair and replace decisions.
CONCLUSION
This article doesn't outline every scenario nor address every aspect of motor management. However, the hope is that this information will be of help in developing more awareness concerning the issue of motor management and its complexities.
A motor management system, functioning at all levels, makes life easier, reduces cost, reduces inventory and reduces energy usage. This keeps everyone happy, including the reliability and testing technician.
Elmer DeForest, CMRP, is a field technician and technology leader for Snell Inspections. This paper was originally presented at Snell’s 2007 Thermal Solutions Conference. To learn more about infrared applications or the conference, call 800-636-9820 or visit www.snellinfrared.com.
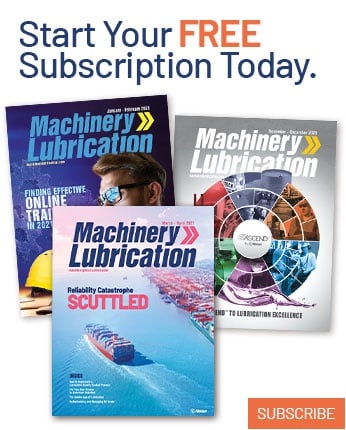