Like many others in U.S. manufacturing, the domestic textile industry has been shrinking dramatically over the past few years — from 1.1 million employees to 760,000 between 2000 and 2005. Amid all the manufacturing job losses, one bright star of an experience sheds some light on improving competitiveness. Here, the textile success story is attributed to lean manufacturing and employee liberation.
A Pittsburgh Inquirer article entitled "N.J. textile mill finds a system for success" reports in detail how a New Jersey-based textile manufacturer is finding ways to compete, “using techniques pioneered by automaker Henry Ford and enhanced years later by Toyota Motor Corporation and others.” The 150-employee firm Absecon Mills Inc. is surviving and, if progress continues, will give workers a share in profits.
Some notable facts about Absecon Mill’s experience:
• Workers brainstorm to improve processes;
• Management sees its job as supporting the workers’ improvements;
• The firm uses help from universities;
• The company cuts out wasted steps, wasted motions and wasted materials;
• Workers occasionally use videotapes to see and study their actions;
• Work flow was changed to reduce the set-up time between jobs;
• The workers measure the time it does take and the time it should take to do a task;
• During brainstorming sessions, typically about 48 ideas emerge; sometimes as many as 60 are voiced;
• Ideas are grouped as high- or low-impact and on how soon they can be acted upon; and
• Quality is a top priority.
In whole, the textile firm attributes its success to lean manufacturing.
There are plenty of lean success stories across plenty of wasteful industries. Yet, the New Jersey manufacturer claims to have seen a 70 percent reduction in waste after only months into introducing lean to its processes. The turnaround began when the company introduced lean manufacturing, aided by $180,000 worth of training grants from the State of New Jersey.
“With the textile industry being assaulted by the Chinese, and the trade agreement expiration in 2005, we need everything we can get,” David Adair, Absecon executive vice president, was quoted as having said in an issue of Upholstery Manufacturing. “The textiles industry is still very much in the 1970s and ’80s. We think that has to change if we're going to stay competitive, or thrive, which is what Absecon is going to do.”
Some results of Absecon’s system:
• Wages are competitive with other industries in the area;
• Orders are shipped within 14 days after specifications are provided by customers;
• The lean approach liberates workers; and,
• By removing the stress from jobs, workers can focus on being creative.
Cutting costs and improving employee morale were part of the strategy, but perhaps more important was completing an order faster than Chinese rivals.
Randolph S. Taylor, chief executive officer of Absecon Mills, tells The Pittsburgh Inquirer, “If Chinese goods are shipped by air freight, the price advantage shifts back to the American market.” Even by air, Chinese mills can't match Absecon's new 14-day response time, he added.
It takes fabric transported from Chinese mills by ship 10 to 12 weeks to deliver product.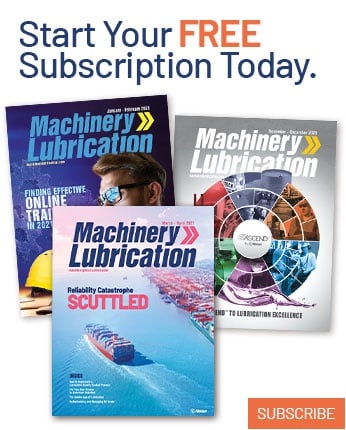