No doubt you've seen the recent news reports featuring Amazon's Prime Air delivery drones. The idea is to get items ordered off Amazon.com into customers' hands within 30 minutes using unmanned air vehicles (UAVs) dispatched from the Amazon warehouse. The drone resembles a giant mechanical insect buzzing through the air with its eight spinning blades.
Despite the skepticism around privacy, safety, reliability and technology, this science-fiction dream is fast becoming a reality. Currently, in Europe alone, there are more than 400 projects in 20 countries to develop unmanned aerial vehicles for civilian use. In late December, the U.S. Federal Aviation Administration (FAA) opened up six sites for unmanned aircraft testing in Alaska, New York, North Dakota, Texas, North Carolina and Virginia.
UAVs are being tested for various civilian uses around the world from inspecting oil and gas pipelines for defects to catching rhinoceros poachers in South Africa. The vehicles move autonomously using GPS, artificial intelligence, video cameras and radar. Advances in modern smartphone technology have helped reduce the cost of the sensors used in UAVs such as accelerometers, GPS and magnetometers, making them more affordable.
The High Cost of MRO Spares
One of the biggest concerns facing manufacturing organizations is having the right parts at the right time when equipment goes down. Maintenance, repair and operations (MRO) parts are often referred to as the "MRO monster" due to the disproportionate effort that is spent searching for and buying parts. The cost of MRO spares can be broken down into five cost types:
1. Carrying costs — Rent, lighting, cooling, staffing, etc.
2. Ordering and acquisition costs — Creating purchase orders, payments, etc.
3. Shortage costs — None in stock, urgent purchases, loss of business or damaged reputation, etc.
4. Obsolescence costs — Parts not used during useful life.
5. Opportunity costs — The costs associated with having money tied up in slow-moving spares.
MRO spares can represent up to 20 percent of total enterprise spending and account for more than half of all indirect purchasing transactions. Many organizations limit the impact of equipment downtime by storing critical spares onsite, but which parts should be held and what are the costs associated with holding them onsite? It's a delicate balance between holding what you need and limiting costs while keeping equipment running.
The stock-turn metric is a good way to determine if you are holding too many spares, while the number of stock-outs tells if you are holding the right spares. Even if you have the part in stores, it could take the technician a long time to find it in a badly organized storeroom. If organizations could eliminate the need to carry spares, calculating these metrics would no longer be necessary.
Parts Delivery by Air
Unmanned aerial vehicles spell good news for the manufacturing industry, particularly for organizations that have cash tied up in MRO spares onsite. Imagine a scenario where Amazon becomes your dedicated parts and spares warehouse. Right now, Amazon has central hubs located close to major cities like Toronto. When equipment goes down, the technician logs onto the company account and places the order for the part to be delivered by air. With 30-minute delivery times expected via unmanned drones, parts could be onsite in the same amount of time it would take for the technician to locate the spare part in the storeroom. The drone would park on the loading dock just like a delivery truck. The part would then be removed from the UAV and installed in the damaged equipment. This would pass along the carrying and obsolescence costs to Amazon, the MRO distributor. Also, any cash tied up in spare parts could be redistributed to other areas of the business.
Shared Inventory System
If many organizations adopt this model, it in effect becomes a shared inventory system where the MRO warehouse becomes the central parts hub for an entire city or locale. As more companies use the service, the MRO distributor becomes incentivized to stock a greater range of parts that serve more customers. In many cases, access to such a large inventory with 30-minute delivery could completely eliminate the decision to hold stock onsite.
Questions to Be Addressed
Obviously, there are a number of concerns that need to be addressed before this could become a reality. What happens if the wrong part is ordered, the drone crashes, the part is delivered after hours when everyone has gone home, or the part is too heavy? We don't want octopods taking over the skies above our cities. While many of the initial concerns are valid, Amazon CEO Jeff Bezos seems determined to iron out these issues and make delivery by UAV part of everyday life. It is just a matter of time before other MRO vendors follow suit.
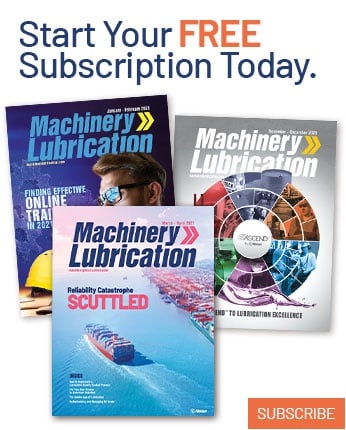