Arizona MEP helps Kiesler Enterprises cut costs and improve delivery
Kiesler Enterprises Inc., a high-end custom cabinetry manufacturer, is known for their exceptional craftsmanship. For more than 20 years, Kiesler has made cabinets for private homes and residential complexes, but they also make kitchen, bath and entertainment furniture of wood and laminate.
Because Kiesler’s designs are so creative and of high quality, the company’s products are in great demand, resulting in a very busy workplace. In order to keep up with such a demand, Kiesler's new management team felt that lean training would help transform their work areas and streamline their production process.
"When our new president, Virland Johnson, and I came to Kiesler, we realized how much the company could benefit with the implementation of lean practices," said Dave Casebere, Keisler Enterprises' chief financial officer. "We consulted with the Arizona Manufacturing Extension Partnership (Arizona MEP), and a project manager met with us to discuss our needs and came back with recommendations."
A core team of employees participated in Time Wise Principles of Lean Manufacturing training, which consisted of both classroom and hands-on simulation to illustrate the basic principles of lean in a manufacturing environment. The response to this training was very positive.
"People were struck by how simple changes like organizing their workspace and providing ideas as part of the solution could bring about such tangible and significant improvements," said Casebere. "Even the shop employees, who are typically very quiet, added their input and felt empowered."
The Arizona MEP staff also took Kiesler teams through a Time Wise Value Stream Management System mapping of their shop floor. This process maps out the existing factory's product and process flow from start to finish, helping to determine a more effective layout. The shop floor was redesigned, and now people and product move through the facility more efficiently.
"We also conducted kaizens, short bursts of activity that result in significant improvements with the team. ThekKaizen process helped redefine the relationship and interaction between sales and drafting. Both departments now combine resources and steps," said Joseph Murcko, project manager for the Arizona MEP. "Orders are completed faster, client delivery has improved, and the company is saving time and money. As the employees see the impact their ideas have, they are eager to keep the momentum going."
"This has been a very successful way for new management to come into a company and win the employees' respect. The lean tools have allowed us to treat the employees as the valuable resources they are," said Casebere. "We hope to continue building on what we have learned as we move on with new projects and improvements."
The Arizona MEP is an affiliate of the National Institute of Standards and Technology (NIST) under the U.S. Department of Commerce. The national MEP is a network of manufacturing extension centers that provide business and technical assistance to smaller manufacturers in all 50 states, the District of Columbia and Puerto Rico. Through MEP, manufacturers have access to more than 2,000 manufacturing and business "coaches" whose job is to help firms make changes that lead to greater productivity, increased profits, and enhanced global competitiveness. For more information on the Arizona MEP program, call 480-874-9100.
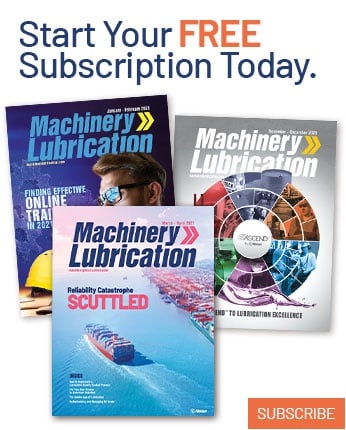