Del Monte Foods is one of the country’s largest and most well-known producers, distributors and marketers of premium-quality, branded food and pet products for the U.S. retail market, generating more than $3.7 billion in net sales in fiscal 2010. With a powerful portfolio of brands including Del Monte, S&W, Contadina, College Inn, Meow Mix, Kibbles ’n Bits, 9Lives, Milk-Bone, Pup-Peroni, Gravy Train, Nature’s Recipe and Canine Carry-Outs, Del Monte products are found in eight out of 10 U.S. households. The company also produces, distributes and markets private-label food and pet products.
The United States Department of Energy (DOE) “Save Energy Now” program completed an Energy Savings Assessment (ESA) two years ago at the Del Monte Foods Plant No. 24 in Hanford, Calif. The DOE Qualified Specialist/Energy Expert conducting the compressed air system ESA was Kyle Harris of Accurate Air Engineering Inc. of Bakersfield, Calif.
The Del Monte Foods plant in Hanford operates three air compressors to supply compressed air to a number of different production end-uses. The compressor system consists of three oil-flooded rotary screw air compressors. All three air compressors are 150 horsepower, with two of the three water-cooled and one air-cooled unit. The air-cooled compressor has been retrofitted with a variable-speed drive. The plant uses compressed air on a schedule of 12 weeks per year, seven days a week, 24 hours per day during the three months out of the year that are considered “peak” production, and a schedule of five days a week, 12 to 24 hours per day during the nine months that are considered “off-peak” production. The peak production period is during the harvest of tomatoes.
As a general rule, the plant most often operates all three air compressors during peak production and the variable-speed air compressor during off-peak production. Currently, the compressed air system average air flow is greater than 1,550 cubic feet per minute (cfm) during peak production and less than 450 cfm during off-peak production. The compressed air system uses more than 980,000 kilowatt-hours per year and accounts for more than 5 percent of the total plant electricity consumption.
ESA objectives
The objectives of the Energy Savings Assessment were three-fold:
- Identify compressed air system improvement recommendations;
- Train plant personnel in how to correctly model the current system; and
- Predict potential savings using the DOE AIRMaster+ software tool.
The focus of the assessment was the compressed air supply, distribution and end-uses.
The approach for the ESA
The compressed air ESA was performed during peak production. Three current loggers and two pressure loggers were sent to the plant more than one week prior to the assessment. At the beginning of the assessment, the loggers were removed and the data was downloaded to a computer. In addition, historical data from a previous study was used to trend the off-peak production periods (nine months). Together, the DOE ESA Expert and plant personnel used LogTool V2 to interpret the data and format the data for direct import into AIRMaster+, a free online software tool that helps users analyze energy use and savings opportunities in industrial compressed air systems. Compressor profiles were developed and a baseline compressed air profile was created within AIRMaster+.
A survey of the compressed air supply and demand was completed. As part of the “training assessment”, the plant personnel, with direction from the DOE ESA Expert, created a number of energy-efficient measures to evaluate the impacts of each measure. Ultimately, these measures were prioritized in order to achieve the best effect of the improvements. A closeout meeting was conducted to present the findings to a number of plant personnel that may be affected by the proposed improvements.
General observations of potential opportunities
The following section briefly discusses the projects identified for additional investigation or implementation. A qualifier is assigned to each project – near-term, medium-term or long-term. These descriptors are identified as follows:
- Near-term opportunities would include actions that could be taken as improvements in operating practices, maintenance of equipment or relatively low-cost actions or equipment purchases.
- Medium-term opportunities would require purchase of additional equipment and/or changes in the system. It would be necessary to carry out further engineering and return on investment analysis.
- Long-term opportunities would require testing of new technology and confirmation of performance of these technologies under the plant operating conditions with economic justification to meet the corporate investment criteria.
Near-term and medium-term opportunities
- Reduce system air pressure: Currently, the system pressure is controlled to 105 psig, while the highest end-use pressure requirements are lower. In addition, the variable-speed air compressor (VFD) was operating a part-load as well as both of the fixed-speed, variable-displacement air compressors. During the assessment, the VFD set point was lowered to 95 psig as well as adjusting the low speed from 30 hertz to 27 hertz. The savings in this opportunity were realized during the ESA. If it is determined that the pressure could be lowered additionally, care should be taken that if a problem is created at a single point of use with the new system pressure, that end-use pressure requirement should be evaluated and modifications made to eliminate the pressure drop through the exiting inlet piping or filter, lubricator, regulator (FLR). It is estimated that more than 99,000 kilowatt-hours, or $9,400, was saved annually, with an immediate return on investment.
- Reduce air leaks: Though the plant currently attempts to address compressed air leaks, it is conservatively estimated that compressed air leaks account for more than 10 percent of the total plant demand. A few obvious and audible air leaks were observed during the ESA, most notably at the de-palletizers. It is estimated that more than 200 cfm in air leaks exist at the plant during periods of production when the plant air pressure is at 95 psig. It is estimated that a minimum of 73,000 kWh, or $6,900 annually, could be saved by reducing the leak load by 100 cfm, with a payback of less than four months.
- Remove open blowing (Line 4): The U.S. Department of Energy (DOE) and the Compressed Air Challenge (CAC) recognize open blowing applications as potential inappropriate uses of “compressor room” compressed air. The choice to use compressed air in these applications is generally because it’s readily available and simple to use but, as a result, overlooks more cost-effective solutions. The CAC promotes plants to use compressed air only if safety enhancement, significant productivity gains or labor reductions will result.
The Hanford plant uses air to blow off the cans prior to coding on most lines. These production applications are perfect examples of DOE and CAC target projects that most often can be replaced with lower-pressure compressed air, increasing the delivered force to application and reducing the amount of compressed air required from the plant air compressors or removed altogether. Assuming the typical quarter-inch blow-off fixture had an air delivery pressure of 200 inches WC in the center of the air stream, an air exit velocity of more than 54,000 feet per minute (fpm) and a consumption of 14 to 18 cfm of compressor room performance, the mass flow of air is 1.32 pounds per minute and the delivered force calculates to 41,347 Newtons of energy. This same application could be replaced with a .52-inch nozzle bore with a 3 psi supply pressure (blower) and supply 52 cfm at an air exit velocity of 35,900 fpm at 78 inches WC. The mass flow of air would be 3.85 pounds of air per minute and a delivered force of 52,611 Newtons. The 3 psi blower supply would represent 28 percent more delivered energy to the process than the plant air blow-off fixture.
The single quarter-inch blow-off on the Line 4 washer is estimated to use 27 cfm of compressor room capacity. During the assessment, it was determined that this application could be removed. It is estimated that more than 6,800 kWh, or $648 annually, was saved by eliminating shutting off the open blowing application.
- Remove open blowing (pre-coders): As explained in the opportunity above, the choice to use compressed air in these applications is generally because it’s readily available and simple to use but, as a result, overlooks more cost-effective solutions. Most often, the coder is placed after the washer and requires that the can is dry prior to coding. In some cases, the coder has been placed before the washer, which eliminates the need to blow off the can. This solution should be investigated for all of the lines. It is estimated that more than 23,000 kWh, or $2,300 annually, could be saved, with a payback of three months.
- Change compressor operation sequence/improve control: The assessment was not able to determine how slow the VFD retrofitted air compressor could operate, though it is suspected it could be turned down to 616 rpm vs. the current 900 rpm. This alone could pay for itself in little time because the air compressor would not run a minimum speed with the plant air pressure increasing. As demand reductions are implemented, the control strategy should be reviewed to insure that the fixed speed units always run at 100 percent, with the VFD unit operating within its turndown range during peak production. If the two fully loaded air compressors and the VFD at minimum speed still exceed the plant demand and the pressure rises, it is possible to run one of the fixed speed units in “Low Demand Mode” so that it loads and unloads while one fixed speed unit operates at 100 percent and the VFD operates within its full turndown to 100 percent. The VFD operation also should be reviewed during off-peak production months. As energy-efficient retrofits are implemented, it is recommended that the compressor controls are evaluated and tuned. Though some data is available, the plant should invest in monitoring both power (kW) and pressure (psig). It is estimated that an additional 24,483 kWh, or $2,400 annually, could be saved.
Management Support
Del Monte Foods is dedicated to reducing energy consumption throughout all of its facilities. The site lead, project engineer Richard Koch provided full support before and during the ESA. Koch is part of the “Energy Team” at the Hanford plant and is dedicated to improve the compressed air system efficiency.
For more information on Energy Savings Assessments through the U.S. Department of Energy, visit the DOE’s Industrial Technologies Program (ITP) Web site at http://www1.eere.energy.gov/industry/index.html.
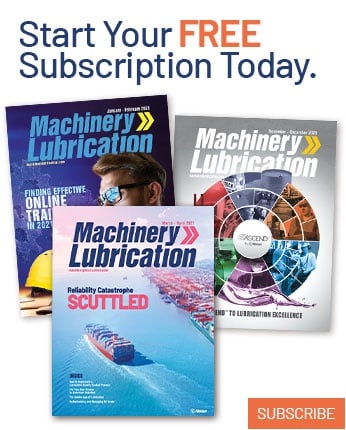