The now bygone era of cheap energy has been replaced by a new reality – steady, steep and continued rises in fuel prices. This has sent plant leaders on a frantic search to find ways to cut costs in virtually every phase of the manufacturing process. One area they may be overlooking is steam generation.
To gauge the high cost of steam trap leakage, consider this example: In just one hour, an unchecked blowing steam trap at 300 pounds per square inch (psi) with an orifice diameter of 3/16 inches will waste 267 pounds of steam. Using an average cost of steam of $12 per 1,000 pounds, one blowing steam trap will expend $77.02 per day, or an astounding $28,110.82 per year.
A recommended first step in determining what your plant might be wasting as a result of faulty traps is to conduct a steam trap survey. Part of this process should involve a review of the steam system itself. Has your system been logically designed but then haphazardly added-on to? If this is the case, you can assume there are problems.
If the steam system is poorly designed, replacing bad traps may only be a temporary solution. Call in an expert if you are unsure about the correctness of your system design. Remember – only an energy-efficient steam system that has been properly designed and maintained will produce and use only the amount of steam needed to get the job done. Here are just a few examples of system neglect:
- Oversized and misapplied steam traps: This condition can cause blowing, leaking and plug dirt.
- Control valves that have been wiredrawn: The valves may be unable to shut as a result of wet steam.
- High back pressure in condensate lines due to blowing traps: This is a situation that can be as hazardous as it is wasteful.
- Low steam temperatures: These are due to traps that are discharging into flooded condensate lines.
- Uninsulated valves, strainers, flanges and even whole sections of steam system piping: This can be a major cause of energy waste.
- Low percentage of condensate return: This is a condition that could escalate the costs of boiler fuel, chemicals, water and sewerage.
The message is clear. Maintaining an efficient steam system will result in savings of energy dollars that can far exceed the costs involved in modifying the existing system.
Small measures can go a long way
Some systems incorporate bypasses around steam traps to temporarily drain systems of condensate while trap replacements are made. While this is a useful practice, there are several downsides to consider. What if the bypasses are opened by operators who believe condensate is not being purged quickly enough? What if they have been inadvertently left open (possibly through operator error)? What if they have not been tightly shut off? What if they are leaking as a result of carbonic acid corrosion? Or, what happens if they are not checked regularly for leakage? The end result can be extraordinarily wasteful and hazardous.
A vacuum breaker is the preventative tool that can put the plant manager's mind at ease. Vacuum breakers allow condensate to gradually drop out of the system. They also help to prevent water hammer, frozen HVAC coils and equipment, as well as the damaging effects of carbonic acid erosion. However, to be effective, a vacuum breaker needs to be installed properly. A steam design expert will help incorporate these indispensable devices into your system.
One of the most simple and overlooked components in a steam system is a strainer with a blow-down valve upstream. Strainers should be installed upstream of all steam traps and other steam components. Steam systems contain iron oxides, which leech out and cause blockage of the strainer. That's why they should be checked and cleaned (blown down) at frequent intervals. Due to potential safety hazards, only those specially trained and authorized personnel, exercising safety procedures prescribed by your company, should be permitted to open these or any other steam valves.
An escalation in condensate temperatures and/or increased flash steam spewing from condensate vent-stacks often signals steam loss. This underscores the need for an ultrasound condition-based maintenance program as a most important component of a steam energy conservation program. Faulty steam traps can be easily detected and corrected with this type of equipment.
How to Test Steam Traps
Online trap inspection usually includes visual, thermal and acoustic means of detection. Visual inspection relies on human eyeballing of a release valve situated downstream of traps, a sight glass or a three-way test valve. With a test tee or three-way valve, an inspector can open these valves and look to see if the trap is discharging condensate or steam.
Thermal inspection involves examination of upstream/downstream temperature variations in a trap. It includes pyrometry, infrared, heat bands (a trap wraparound that changes color as temperature increases) and heat sticks (which melt at various temperatures). As a steam trap begins to leak steam into the condensate system, the temperature on the discharge side of the trap increases. If only one failed open trap discharged steam into a sufficiently vented and appropriately sized return system, there would not be an appreciable difference in condensate system temperatures. However, if the failed open trap raised the pressure in the return line in a poorly designed and restricted system, higher temperatures would result.
The temperature method depends on identification of this temperature variance. But the downside is that this temperature testing method does not work well most of the time because multiple traps usually feed into a common return. When those traps fail, they pressurize the common return header. Since the failed open traps dump into the common return, pressure will equalize in the condensate system. As a result, the same temperature will be read on the discharge of all sections of the return system. Therefore, temperature testing under these circumstances often provides inconsistent results.
Acoustic techniques require an inspector to listen to and detect steam trap operations and malfunction. This method includes various forms of listening devices, such as mechanics' stethoscopes, screwdrivers and ultrasonic detection instruments. The most advantageous listening device will allow users to listen to the sounds of steam trap operations while isolating most ambient system sounds. The ultrasonic leak detector is the easiest to use and provides the most accurate of the sound testing methods. Ultrasound detectors are sensitive to high-frequency (short-wave) signals; they tend to ignore most stray piping system signals. Also, they are very directional in their pick-up.
For this reason, they allow users to hear and see on display panels the exact functions of steam traps.
Ultrasonic detectors generally have a stethoscope (contact) module, which contains an ultrasonic transducer attached to a metal rod that acts as a “wave guide.” This sensor is touched on the downstream side of a trap to determine mechanical movements, or steam and condensate flow. Most ultrasonic detectors amplify the signals and translate them into the audible range where they are heard through headphones or seen as intensity increments on a meter. Some include frequency tuning to allow users to tune into desired trap sounds.
When utilizing the ultrasound method, the tester must have knowledge of the steam system application and trap type being used. Ultrasonic instruments should also be used in conjunction with an infrared detector so that partially or fully blocked traps are easily identified. Infrared temperature instruments will also identify increased back pressure in condensate systems. Escalations in condensate temperatures not only adversely affect the performance of otherwise properly functioning traps; they create an assortment of detrimental effects to the overall steam system.
Conclusion
The days of cheap energy are over, and there is strong likelihood that fuel costs will continue to escalate. It is imperative that a steam system be regularly monitored for loss and, if necessary, redesigned or replaced – not only for the sake of producing quality products efficiently and cost effectively, but for survival in today’s highly competitive environment.
About the authors:
Bruce Gorelick is the vice president of Enercheck Systems of Charlotte, N.C. Alan Bandes is the vice president of marketing for UE Systems of Elmsford, N.Y. For more information, visit www.enerchecksystems.com and www.uesystems.com.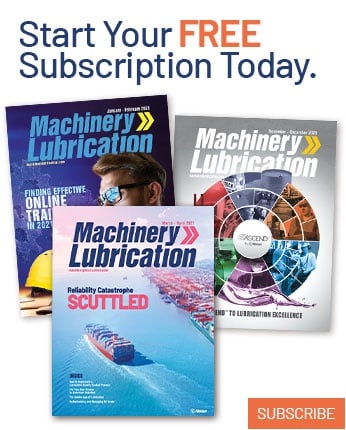