Ask the Energy Expert is an ongoing column with the intent of providing information and solutions for industry’s most pressing questions. This issue’s Energy Expert is Brad Runda, the energy manager at Saint-Gobain.
Dear Energy Expert:
Not only is your company a Save Energy Now LEADER, but it was named Energy Star Partner of the Year two years in a row, and your plants have been recognized as Energy Savers and Energy Champions. What can my company do to be as successful?
What follows is Brad’s response:
Saint-Gobain is a global manufacturer and distributor of flat glass, building products, glass containers and high-performance materials.
With more than 1,000 subsidiaries in more than 50 countries, it is the world’s largest building materials company and a leading distributor of building products. Founded in 1665 and headquartered in Paris, Saint-Gobain had worldwide sales of $53 billion in 2009 and employs approximately 190,000 people.
Saint-Gobain Corporation, based in Valley Forge, Pa., is the holding company for the U.S. and Canadian-based operations of the global Saint-Gobain Group.
The company manufactures a range of building products, high-performance materials, and glass containers at more than 140 plants throughout North America. The company is also a distributor of building materials, with more than 160 outlets throughout the United States.
Background
Saint-Gobain has long adopted a corporate philosophy of energy efficiency that is demonstrated throughout the company, such as in the construction of energy-efficient buildings and in making the plants that produce materials for those buildings consume energy more effectively while reducing related carbon dioxide emissions. The company even implemented a program to train contractors on energy-efficient construction and explain how they can apply those techniques when constructing new residential facilities.
To date, six of Saint-Gobain’s U.S. plants have participated in U.S. Department of Energy (DOE) Energy Savings Assessments (ESAs), with many of those plants formally being recognized as Energy Savers and Energy Champions for reducing their energy consumption a minimum of 7.5 percent since participating in an ESA. Saint-Gobain also was named the U.S. Environmental Protection Agency’s Energy Star Partner of the Year for the last two years. Saint-Gobain received the honor in 2010 because the company reduced its North American energy consumption 2.2 percent and lowered its carbon dioxide emissions by more than 70,000 metric tons.2
In November 2009, Saint-Gobain partnered with the DOE Industrial Technologies Program (ITP) to become a Save Energy Now LEADER and was one of the first companies to take the voluntary Pledge of reducing its energy intensity at least 25 percent over the next 10 years. As a LEADER, Saint-Gobain is increasing its energy efficiency target and is now eligible for priority access to ITP tools and resources for industrial energy efficiency.
Preparation is Key
As part of an overall strategy to improve energy efficiency, Saint-Gobain facilities are encouraged to specifically prepare for and participate in energy assessments. Proper planning helps ensure implementation of the recommendations that result from those assessments. Saint-Gobain shared some tips during the January 2010 Save Energy Now LEADER Webinar, led by Brad Runda.
Plan
The first step is to set aside some time to prepare for an energy assessment, whether it is a Save Energy Now ESA or Industrial Assessment Center-conducted assessment. Proper preparation will help to minimize the amount of downtime that may occur and will help to avoid a drop-off in momentum.
Prepare
Saint-Gobain believes that thorough preparation before an assessment will yield the maximum results from the assessment – including successful implementation. In order to optimize the time of an Energy Expert or Qualified Specialist during an assessment, Saint-Gobain recommends the following steps before the assessment commences:
-
Safety Review: Safety is the top priority for anything related to the plant. It remains the top priority before and during an assessment, so a safety review with people participating in the assessment is a must.
-
Internal Approval: A key step is to receive internal approval for the people participating in this assessment. This is also a good opportunity for establishing goals and determining your measures of success during and after the assessment.
-
Confidentiality Agreement: This is a fundamental requirement before any assessment. When signed, this will ensure that process-specific information and other sensitive information can be shared with the assessors, enabling them to have access to the information they need to do their job properly.
-
Fuel Consumption: It is imperative to compile your natural gas and electricity bills over the last year (data for the past two years is even more helpful). These bills will provide the assessor with an accurate history of the plant’s energy consumption and enable that assessor to identify patterns or notable changes in consumption. It is also beneficial to know where and how energy is consumed, as this helps those conducting cost benefit analyses. Being armed with these details will help when selecting which piece of equipment or system should be analyzed during the assessment.
-
Metering: If available, submetering and load profile information are important to have on hand during an assessment and should be compiled before the assessment begins. An energy manager must determine and prepare locations for metering if the plant does not already have it. It is further recommended to work with the person conducting the assessment to determine where it should go.
-
Equipment and Processes: Energy managers should know where equipment is located; blueprints and diagrams are helpful for this. Energy managers should also compile a list of equipment and its purpose, as well as original equipment manufacturer specifications. Further, the energy manager should know process requirements and communicate any needs of the plant to the energy assessor. Understanding the plant’s needs and goals will help the energy assessor identify energy efficiency improvements or process changes that can help fulfill those criteria.
Corporate Buy-In
When trying to receive corporate buy-in for implementing energy efficiency projects, it is important to emphasize how the company and the individuals in charge will benefit. The energy assessor may provide suggestions for potential financing, but it is important to check other places for more information to really understand what options are available to implement the project. It is also important to develop a strategy for presenting recommendations on which projects should be implemented, be it prioritized by cost savings or return on investment. “Low-hanging fruit” opportunities should always be included, because they have an immediate payback and motivate staff to look for additional opportunities.
Capital Budgets
An energy manager needs to understand how his or her company’s budgeting process works to be able to utilize capital and ensure funding is set aside for energy efficiency projects. If an assessment is pending during the time budgets are being developed, a placeholder can added to reserve funds for implementation. It is also important to check the status of the capital budget periodically to determine if there are project offsets or unspent money that can be allocated to fund some of the energy efficiency improvements identified during the assessment.
Staff
Determine correct participants and their roles in the process. Having the right people participate in the assessment is the key to success. It is important to receive a commitment from both personnel and their managers before getting started to ensure a successful assessment.
Conclusion
Saint-Gobain’s commitment to energy efficiency has been showcased through the organization’s voluntary commitment to reduce its energy intensity 25 percent over the next 10 years through ITP’s Save Energy Now LEADER program. The company’s proven approach to improving the odds of a successful assessment and implementation can help others be successful as well.
This article appeared in the Spring 2010 issue of the U.S. Department of Energy’s Energy Matters newsletter. For more information on the DOE and its Industrial Technologies Program, visit http://www1.eere.energy.gov/industry/.
Endnotes
1 Saint-Gobain. Saint-Gobain at a Glance. http://www.saint-gobain.com/en/press/saint-gobain-glance. Visited 29 March 2010.
2 Energy Star. Saint-Gobain: Energy Star Partner of the Year. http://www.energystar.gov/index.cfm?fuseaction=pt_awards.showAwardDetails&esa_id=3656 . Visited 29 March 2010.
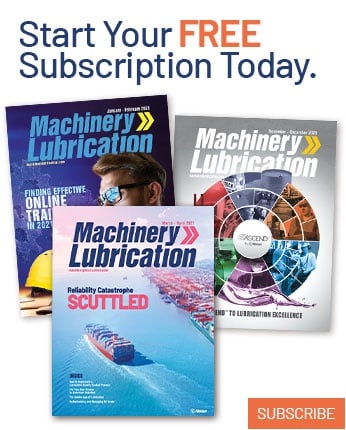