Over the past decade or so, we have had many occasions to single out the “best of the best” in reliability engineering. These companies are progressively shifting from traditional time-based maintenance and even from generally advantageous predictive maintenance (PdM) to the best possible approach: selective upgrading.
The role of service providers
Like their less sophisticated competitors, even the “best of the best” gravitate toward service providers. But the best of the best involve the service provider in life cycle cost (LCC) studies and will not hesitate to upgrade to better products when LCC numbers point in that direction. We feel vindicated by these trends because it was clear 30 years ago that buying bearings or seals from a vendor/manufacturer with strong application engineering support paid handsome dividends. Optimistic maintenance cost-reduction goals were primarily achieved when best-of-class companies bought bearings and sealing products from sources that showed them how to avoid repeat failures. Tapping into their time-tested areas of expertise was always worth the incremental cost over purchasing from “lowest bid” sources.
We also found networking helpful in recognizing failure trends and, occasionally, other disturbing patterns. A network colleague of ours makes his living as a process reliability engineer in one of the North Central states. He recently connected the dots when he briefed us on failure patterns. He and a few others are clearly in the forefront of failure analysis developments. Hopefully, they are the trend of the future. And so, we certainly believe the most successful service providers will float to the surface because they will listen to the advice of people who make it their goal to add value and maintain an unswerving sense of self-worth.
Repeat failures tell an important story
The process reliability engineer who connected the dots defined repeat failuresas recurring difficulties that prevent equipment from achieving its anticipated life expectancy. Repeat failures exist because we have perhaps concluded that a particular failure mechanism is more economical to manage than to correct. If allowed to persist, a repeat failure will eventually be perceived as a discretionary, low-risk nuisance with no potential safety or environmental consequence. This defective risk assessment approach is defined as “normalization of deviance” and must be resisted.
He went on to describe as an extreme failure an explosion, fire, wreck or crash – something with devastating consequences. He documented the role a repeat failure plays in the life cycle of an extreme failure and convinced me that repeat failures are the likely intermediate step leading up to an extreme failure. Even more importantly, repeat failures also are reliable warning signals that can be spotted before many catastrophic equipment failures occur. Taking control over repeat failures to consciously prevent a catastrophic accident reinforces the precept that we are in charge of equipment reliability and not victims of “unpredictable” behavior.
Repeat failures build a reactive work order history in our maintenance management systems. More often than not, the entries abound with useless information such as “bearing replaced” when the entry “bearing failed due to oil starvation resulting from use of pressure-unbalanced constant level lubricator” would have added real value. But that’s another story, and it simply illustrates that managing maintenance costs and failure avoidance are far from the same. In any event, repeat failure work orders tend to get buried under higher-priority items that represent a more immediate production constraint.
Repeat failures often are addressed only as time allows and without asking why the failure occurred. Knowing why the failure occurred may require a failure analysis – and performing a failure analysis on something viewed as a low-consequence risk takes time away from addressing immediate production constraints that show up on the daily maintenance plan. In truth, this highly reactive and inappropriately labeled “reliability strategy” is the trademark of a repair-focused organization and should be questioned. While they might claim to be reliability focused, such organizations exhibit few, if any, of the requisite traits; they perform reliability engineering in name only.
And this is where we come full circle. We must realize that the most successful employees and service providers will add value every step of the way. As individuals and companies, they will do everything possible to be better than average. It will serve as a protection to them as individuals and companies to be more dependable, more accurate and more knowledgeable than the rest of the crowd.
In a process industry environment, these persons, business entities and organizations will view every maintenance event as an opportunity to upgrade. Upgrading means recognizing and strengthening the weakest link in the component chain, whenever cost justified. Doing so will make the operator’s life easier and enhance his and her sense of self-worth. It will open wide the (presently narrow) door to operator-driven reliability (ODR). Conscientious upgrading includes diligently performing structured failure analysis. So, going beyond traditional maintenance is far more important than most might think. It’s time for a fundamental change in the flawed thinking that has left us with unacceptable risk in uncertain times.
To summarize the points:
- We must stop conducting business as usual.
- Merely paying lip service to reliability improvements is a disservice that must be exposed.
- Inquest must precede remedial action; remedial action without inquest will result in repeat failures.
- Repeat failures precede extreme failure, and extreme failures are disasters.
- Show extreme resolve to not become part of this destructive and negative chain of events.
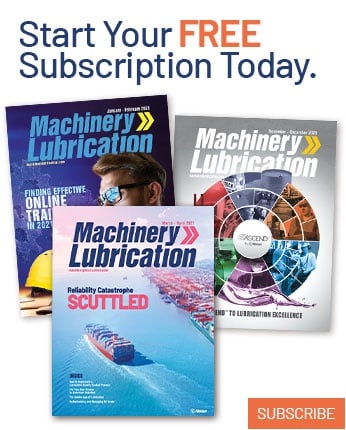