Reliable technology is essential to maintaining peak performance for plant operations. The problem for many companies is determining how to make major technology upgrades while minimizing risk, avoiding extended plant shutdowns and maximizing the return on investment. This was the situation facing Hill’s Pet Nutrition, a leading supplier of premium pet food products.
Hill’s was founded more than 50 years ago by one veterinarian’s unique commitment to pet nutrition and well-being. Today, Hill’s pet food products are available in 86 countries around the world, with sales totaling more than $1 billion. The company is one of the largest employers of veterinarians, with more than 150 veterinarians, nutritionists and food scientists on staff. In fact, veterinarians worldwide recommend and feed their own pets Hill’s products more than any other brand of pet food.
The challenge
In 2006, the plant began to recognize a need to upgrade its existing I/O system, which had been in place for more than 20 years. The problem centered primarily on periodic failures involving the analog inputs. Maintenance would have to go out to the I/O rack, unplug the card and reconnect it, all to have the module start working again.
“All of our process control for the extruder line is communicated through the analog input, so when that communication fails, it essentially shuts down the process,” said Shane Simmons, systems engineer, Hill’s Pet Nutrition. “Once the extruder line shuts down, it can take up to an hour and a half to reconfigure the system and bring the process back online.”
Additionally, finding replacement cards was becoming more difficult, since the vendor was no longer making them. The only other option was to have them repaired, which posed additional challenges in terms of potential delays and added cost.
Another concern centered on the various controllers the plant employed throughout its production operation, including disparate controllers on its raw materials, extrusion and packaging lines, as well as dual controllers on its batching line to maintain a tight tolerance on its ingredient mixing process. Unreliable service, declining operator knowledge, and increasing maintenance and support costs were pointing to a strong case for a control system migration.
“With the ongoing reliability issues from our I/O system and the existing controllers nearing the end of their technology life cycle, we realized it was time for a major upgrade of both platforms,” Simmons said. “We needed a flexible, high-performance control system that could be integrated into our existing infrastructure with minimal impact and provide a technology framework that would allow us to grow well into the future while protecting our past investment.”
Perhaps the biggest challenge was determining how to implement a simultaneous upgrade of both platforms in a way that would help minimize the impact on production. Maintaining plant uptime was critical since delays would reduce the amount of product packaged and shipped to customers. Engineers determined that the best strategic approach would be to implement the upgrade as part of a multiphase process, especially considering the plant’s intense production demands and the potential impact on multiple lines.
The solution
To meet its long-term control system needs and help minimize the risk to its production operation, Hill’s turned to Rockwell Automation and its Allen-Bradley ControlLogix programmable automation controller (PAC). A key factor in the decision was the ability of the ControlLogix PAC to scan the existing I/O cards while also communicating with the other controllers in the plant. This solution offered the manufacturer a cost-efficient way to convert its existing I/O to the Allen-Bradley Flex I/O platform as part of a multiphase implementation.
The first phase began in early 2008 with the conversion of the first of its four extruder lines to the ControlLogix PAC technology. With the ControlLogix PAC, engineers simply unplugged I/O from the existing system and plugged it into the ControlLogix PAC to test it on weekends. Then, the engineers would plug it back into the original system with minimal impact on production during the week. This helped minimize the amount of downtime required while allowing a phased upgrade.
“That was probably one of the biggest factors that sold this project,” Simmons said. “Implementing this conversion did not require taking the line down for a minimum of six months to a year to replace more than 10 I/O racks, which would be completely unacceptable for our operation due to the high cost of downtime.”
Allen-Bradley technology also offers long-term support, favorable total cost of ownership, and the extensive support capabilities of Rockwell Automation, including a well-defined and strategic technology migration path.
The upgrade to the ControlLogix PAC also will allow the plant to move toward standardizing on EtherNet/IP network communication. Currently, the plant maintains multiple networks, including DeviceNet, Modbus Plus and Data Highway Plus. Narrowing these down to a single network architecture will help the plant simplify maintenance and troubleshooting, and lead to better plant-wide integration. Adding to the ControlLogix PAC benefits, migration enablers also played a key role in the Hill’s phased approach. Two migration enablers were used, the Automation Network X-change (AN-X) module provided by Quest Technical Solutions, a Rockwell Automation Encompass Partner, and the Modbus Plus dual-port communications module by ProSoft Technologies.
The AN-X module serves as a database for all the I/O and ControlLogix PAC interface, linking and mapping them together in a seamless fashion. This module, which replaced an existing I/O scanner, automatically reads all of the I/O card information and passes the information to the ControlLogix PAC via Ethernet, providing plant-wide communication capabilities. It also offers new tags that can be imported into the Rockwell Software RSLogix 5000 programming software, which allows for easier reference to specific I/O data in the controller.
The Modbus Plus dual-port communications module acts as an I/O module between the existing Modbus Plus network and the ControlLogix controller backplane, allowing easier access to processor memory for data transfer between process and module. A 4,000-word register space in the module exchanges data between the ControlLogix PAC and the existing network, allowing the ControlLogix PAC platform to connect directly on to the existing network as a peer.
Ladder logic is used for data transfer between module and PAC, and configuration data is obtained through user-defined ladder. Other potential Hill’s applications include the connection of ControlLogix controllers to Modicon controllers, and the connection of Modbus Plus speaking devices such as drives, relays and power monitor hardware to the Rockwell Automation controller backplane.
The results
The continued upgrade of the first extruder line will involve converting the existing controller to the ControlLogix PAC, along with about 10 I/O racks to the FLEX I/O platform. The existing Modbus Plus network will eventually be replaced with EtherNet/IP. Also, as variable frequency drives in the plant are updated, they will be replaced with the new company standard: the Allen-Bradley PowerFlex 70 drives.
By reducing its I/O reliability issues and reducing the downtime, the plant anticipates a productivity increase of approximately 5 percent. In addition, the high-speed processing capabilities of the ControlLogix PAC will allow the plant to replace the two controllers currently installed on its batching line with a single controller. This, of course, means less space needed and a less complex system.
After implementing the ControlLogix PACs, the plant will have access to reliable local support in Bowling Green through its local Allen-Bradley distributor, as well as through the extensive support capabilities of Rockwell Automation. This is especially crucial when it comes to programming support. The ControlLogix PACs use the standard RSLogix 5000 programming package, which provides a more user-friendly programming environment compared to the previous system.
“Finding a knowledgeable programmer on short notice can be a challenge, especially in this area of the country,” Simmons said. “Locating programmers for Allen-Bradley controllers has been a much easier proposition – we’ll have a lot more options now.”
The RSLogix 5000 software features add-on instructions, which allow engineers to create sets of commonly used custom instructions that can be easily reused without modification. This allows the plant to create standardized libraries that can help reduce programming time and provide consistency to help simplify troubleshooting and reduce training costs.
“Different contractors working on multiple processors throughout the plant resulted in a variety of software code being developed over the years, which increased programming complexity and the need for more specialized software expertise,” Simmons said. “Now when we program across the plant, more of our code will look the same, providing engineers with more standardized instructions and greater consistency between systems.”
In addition, the tag-based programming inherent in RSLogix 5000 software will allow the plant to keep its current I/O wiring configuration in place without changing a lot of field devices, which will help save a major amount of configuration time and cost.
“With ControlLogix PACs, we’re confident that we now have a stable, long-term migration path that will allow us to protect our investment and scale the technology to meet our long-term needs,” Simmons said.
The upgrade project will be implemented in phases over five years and will involve upgrading a minimum of six of the plant’s existing controllers, including a DCS system, PLCs and motion controllers, to the ControlLogix PAC platform. The upgrade will involve all of the plant’s major production lines, including four extruder lines, a raw ingredients line, batching line and packaging line.
The company also is using this project as a model for its other plants, including a new plant in Emporia, Kan., that will be based on the ControlLogix PAC technology.
“This project is the proving ground for that plant since they are incorporating a lot of our specifications and following very closely what we’re doing at this site,” Simmons said. “We’re leading the way in terms of defining our new technology roadmap.”
For more information on Rockwell Automation products and solutions, visit www.ra.rockwell.com.
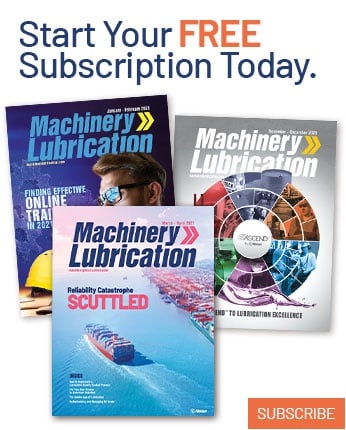