The slings that cranes use to hold suspended loads are also a key element in this kind of material handling. Slings are made of a variety of materials. We determine what type of sling to use by the size and type of load, and the environmental conditions in the work area.
For cranes and slings to perform properly, they have to be in top condition. So, good inspection and maintenance are especially important.
Let’s review some of the key safety issues related to cranes and slings. We'll talk about how to select and use them, and how to identify equipment that needs replacement or repair. Our goal is to use this expensive and essential equipment correctly and maximize its useful life.
General hazards
There are two main hazards when we use cranes and slings:
1) Dropping the load.
2) Hitting someone with the load or the equipment.
We also want to avoid damaging the load or the equipment itself. That can be very costly both in terms of equipment repair and replacement and in our ability to meet our productivity and quality goals.
These hazards are present any time we skip a step or ignore a problem at any point in the inspection, maintenance and use of this equipment. To avoid danger to the operator and others in the crane's vicinity, we all have to understand the safety procedures and follow them closely.
OSHA regulations
OSHA has very detailed rules governing the selection and use of cranes and slings (29 CFR 1910.179, 180, 184). We can't begin to cover every point, but we will look at some of the most important. OSHA issues many hundreds of citations for violating these regulations each year, though they don't rank in the agency's "top 10." Most citations relate to equipment inspection – an area where it's very dangerous to fall short. As we'll learn, OSHA is very specific about what we must inspect frequently (sometimes daily) and what requires periodic inspection. To prevent accidents with cranes and slings, you need a combination of thorough inspection, trained and skilled operators, and safety-conscious employees.
Identifying hazards
The best way to identify a crane and sling hazard is to keep your eyes open. Anyone who works around an operating crane has to be constantly aware of its movements. Stay out of the way of the machine and its moving parts. If the operator sounds the crane's warning signal, get out of the way fast. It's also a good idea to become familiar with the crane signalman's hand signals. They're much like the ones used by traffic cops and can alert you to the crane's movement.
The other key to potential crane and sling hazards is the equipment's rated capacity, or the maximum load it can handle safely. OSHA, the company and good sense prohibit overloading, because it could make the crane overturn or drop its load. Equipment manufacturers rate each piece of equipment in terms of how heavy a load it can carry. OSHA requires the rated load to be "plainly marked" on each side of the crane, as well as inside the cab where it's visible to the operator. If a crane has more than one hoisting unit, the hoist or load block also has to be marked with the rated load. You have to be able to read this rating from the floor or ground.
Slings also have rated capacities that you can't go over without violating OSHA rules and putting people in danger. Manufacturers must attach permanent, durable rating information to alloy steel chain slings, along with their size, grade and reach. The maximum load capacity for wire rope, natural fiber rope and synthetic fiber rope slings is set out in a series of charts in the OSHA regulation, based on size, construction, etc. On metal mesh slings, some type of durable marking also identifies rated capacity for several different types of hitches. Synthetic web slings have markings or codes to show rated capacities for each type of hitch and type of synthetic web material.
Slings also have limitations as to the temperatures they can handle, and the environmental conditions in which they can be used safely. Check all these restrictions carefully before choosing or using a sling.
Protection against hazards
Cranes and slings are designed and built to help protect both operators and those in the area from hazards. In addition, OSHA prevents equipment use rules that should prevent accidents. Here are some OSHA crane safety requirements that help protect the operator:
n Rigid, secure permanent ladders or stairways with anti-slip surfaces go from the ground to a gantry crane's footwalk or cab platform.
n Rigid, sturdy crane footwalks with anti-slip surfaces are used for cranes with enough headroom.
n Electrical equipment, located a safe distance from live parts, is guarded and protected from dirt, grease, oil and moisture.
n Devices will disconnect all motors and prevent accidental restarts when power fails.
n A fail-safe responds to any automatic crane operation malfunction.
n Power supply switches or circuit breakers can be readily opened, locked open and disconnected as needed.
Other OSHA crane safety requirements help protect everyone in the area. For example:
n The operator can reach operating handles easily in all positions while having a full view of the load.
n The crane maintains at least 3 inches overhead clearance and 2 inches lateral clearance from any obstructions, and 3 inches clearance between the cab and any fixed structure.
n Moving parts are guarded.
n Each independent hoisting unit has one or more self-setting brakes.
n The drum has at least two wraps of rope when the hook is in its lowest position; a clamp or socket securely attaches the rope to the drum.
n An appropriate fire extinguisher is readily available.
Safe crane operation
All these built-in protections are just the start of crane safety. A skilled, safety-conscious operator has to be able to lift and handle loads without creating a risk to the materials or the safety of other workers. Without covering every detail, let's look at this job. You'll see why we can't let just anyone operate a crane.
To prevent overload, the operator has to check equipment load capacity and the weight and shape of the load. Even this isn't simple, as limits on some cranes are affected by boom length and radius.
The actual operations require a lot of precision. Before lifting, the operator brings the hook over the load, making sure that it's not swinging. Slings or other approved devices attach the load to the load-block hook. Then, the operator checks that the hoist chain or rope has no kinks or twists and isn't wrapped around the load. If the load has sharp edges, it has to be padded to prevent cutting the slings.
If the load is close to the rated capacity, the operator has to test the brakes by raising the load a few inches and then braking. Even organizing the inside of the cab takes thought. To give the operator as much working space as possible and protect those below, OSHA requires operators to store clothing and other belongings out of the way. Tools, oil cans, waste, etc., must be kept in the tool box. Once all the checks are complete and there's no one on the load or hook, the operator's skills get a real workout. OSHA specifically requires operators to stay at the controls while the load is suspended and to "avoid carrying loads over people." The operation must be very smooth and careful, avoiding sudden starts and stops as well as any contact with other equipment, materials or people.
Operating slings safely
The operating requirements for slings begin with choosing the best sling for the job. As mentioned earlier, you have to consider the load's size, weight, shape, temperature and sensitivity as well as the environmental conditions in the area. Alloy steel chain slings are strong, able to withstand very hot temperatures. They adapt well to different load shapes but can, however, be damaged by sudden shock.
Wire rope chains are available with two types of cores. Those with fiber cores are flexible but less resistant to environmental damage. Wire rope cores are stronger and better able to resist heat. Fiber and synthetic rope slings are used for temporary and marine work. They're also often a good choice for expensive loads, highly finished or fragile parts, and delicate equipment. Never use fiber rope if there's a risk of exposure to acids or caustics. You even have to consider which types of synthetic match the hazards. Use nylon for alkaline or greasy conditions and when resistance to chemicals or solvents is important. Dacron is best for high-temperature bleach solutions or high concentrations of acid solutions. Use polyester for acids or bleaching agents or where you want to keep stretching to a minimum.
While tightening a sling, OSHA warns against placing hands or fingers between it and its load. Here are some other OSHA requirements to keep slings from breaking or causing accidents:
n Never let a sling kink or shorten it with knots, bolts or other makeshift devices.
n Balance loads and attach them securely.
n Pad or protect the sling from sharp edges.
n Keep suspended loads away from all obstructions.
n Stay away from other employees while lifting and holding suspended loads.
n Don't drag a loaded sling along the ground.
n Don't pull a sling from under a resting load.
To hook up a sling, the crane hook must be right over the load's center of gravity, so it won't tilt and cause unequal stress in the different sling legs. The heavier the load, the more important it is to distribute it among more sling legs. The operator has to position the hook directly over the load and seat the sling squarely within the hook bowl. Slowly, the operator takes up the slack in the sling, continually checking its tension. It's important not to raise the load more than necessary or leave it suspended in the air.
Safety procedures
OSHA divides inspection requirements for cranes in regular use into two categories: frequent (daily to monthly) and periodic (one to 12 months). You might have to step up inspections for equipment that's near the end of its useful life. You must inspect cranes for any defects that might be a safety hazard. Here are OSHA's time frames and some things to look for:
Daily: operating mechanism maladjustments; deterioration of air or hydraulic line, tank, etc.; deformed or cracked hooks; worn, twisted, or stretched hoist chain.
Monthly: rope condition; deformed or cracked hooks and hoist chains. These inspections must be certified, dated and signed.
Frequently: excessive component wear on functional operating mechanisms; rope reeving.
Periodically: deformed, cracked or corroded members; loose bolts or rivets; cracked or worn sheaves or drums; worn, cracked or distorted pins, gears, and other parts; excessive brake system wear; indicator inaccuracies; power plant performance; chain drive sprocket wear and chain stretch; pitted or deteriorated electrical apparatus.
There are similar inspection requirements for cranes not in regular use. In addition, new or altered cranes must be tested before use, and ongoing maintenance must follow the manufacturer's recommendations. Crane repair or maintenance has to be performed in a location out of harm's way. Before starting, you turn it off, lock the main or emergency switch open, and put up warning or "out of order" signs. You can't always fix crane parts. OSHA says to discard crane hooks that show defects; defective load attachment chains and rope slings; cracked, broken, bent or excessively worn critical parts.
You also can't use a rope if damage could reduce its strength and cause a safety hazard. Be alert for these danger signs: wire wear or corrosion that reduces its diameter; broken or worn outside wires; broken or corroded end connections or wires; severe kinking, crushing, cutting or unstranding.
Sling inspection
OSHA also emphasizes careful sling inspection. After all, they have to connect the load to the material handling equipment. The agency requires "a competent person designated by the employer" to inspect each sling and its fastenings and attachments for damage or defects each day before use. "Damaged or defective slings shall be immediately removed from service," OSHA states.
In addition, inspect slings at least yearly for a variety of defects, backed by a written and dated record. More frequent inspections may be needed, depending on the amount and severity of the sling's use. Obviously, remove a sling with defects or deterioration from service. OSHA even defines how much deterioration or distortion can place a sling out of service. Here is some of what OSHA says to check.
Alloy steel chain sling inspections look at wear, defective welds, deformation and increase in length. You can't use a sling with cracked or deformed links or other components. Get rid of either alloy steel or wire rope slings if hooks are cracked, opened more than 15 percent of their normal narrowest opening or twisted more than 10 degrees. Wire rope slings are especially sensitive to misuse or abuse. Don't use one if you spot severe corrosion; shiny worn spots on the outside; a loss of one-third in outer wire diameter; damage or displacement of hooks, rings or other end fittings; distortion, kinking or other damage to wire rope structure; or excessive broken wires. Also remove a sling from use if it's exposed to temperatures of 200 degrees F or higher or there's evidence of heat or wire rope structure damage.
With these cautions in mind, it's interesting to note that wire rope slings that are used more will usually last longer. They may, however, need extra lubrication, especially if they carry heavy loads, have a number of bends or operate under difficult conditions. Store these slings in a dry, well-ventilated building or shed. They could corrode or rust if they're left on the ground or exposed to weather. Don't use a metal mesh sling when an inspection reveals these problems: broken weld or brazed joint along the edge; reduction in wire diameter of 25 percent from abrasion or 15 percent from corrosion; lack of flexibility; or distortion of either handle.
When you inspect natural and synthetic fiber rope slings, look for abnormal wear. Dry, brittle, scorched or discolored fibers could be signs of trouble. So can powdered fiber between inside strands, broken or cut fibers, variations in strand size or roundness, or distortion of hardware. OSHA states firmly that you may not use a repaired or reconditioned fiber rope sling. Don't use a synthetic web sling that's damaged by acid or caustic burns. Other fatal problems include melting or charring, snags, punctures, tears or cuts, broken or worn stitches, or distorted fittings.
Conclusion
Material handling is a complicated task that requires plenty of skill, whether you're doing a manual lift or working with cranes and slings. You can't be too careful when you use cranes and slings, and OSHA's rules on safe operating practices are very specific.
You also can't be too careful when you inspect the equipment. Just the length of the list of defects that can put the equipment out of service points out how critical it is to make each inspection thorough. You can't just look at a sling and pronounce it "fine." If you do, you're violating the law and putting a lot of people and some very expensive equipment and loads at risk.
If you are involved with any tasks that relate to cranes and slings, take them very seriously. It's a great responsibility. Even if you don't work directly with this equipment, we hope this meeting has opened your eyes. Though they're designed to handle heavy loads, cranes and slings are really precision equipment. Every part, every fiber, has to be in top condition and used with skill and care or the whole operation can fail – with potentially hazardous results.
About the author:
This article provided by TrainingOnline.com, an e-learning division of Business and Legal Reports Inc. and a publisher of quality compliance, training and productivity tools for the workplace. For more information on the company’s range of products and services, visit www.TrainingOnline.com.
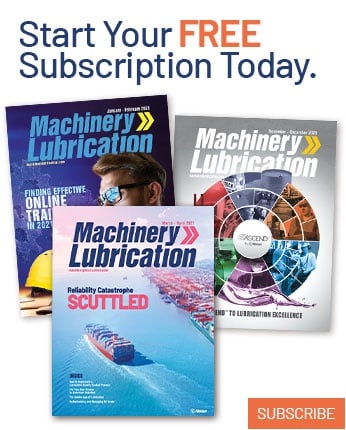