As Owens Corning tests the elements of the Superior Energy Performance framework in its Waxahachie, Texas, manufacturing plant, the company is finding that the program complements its existing plant Operations Management System and supports long-term energy-reduction goals. In this interview, plant leader Glenn Haley fields questions about his facility’s experience in testing the program, and shares lessons learned in the process of developing a sustainable energy management program at Owens Corning.
Question: Tell us about your plant’s energy management program.
Answer: First of all, we have incorporated the American National Standards Institute (ANSI) MSE 2000-2008 energy management standard into our Operations Management System (OMS). We are already an International Organization for Standardization (ISO) 9001 plant, and we chose to build our OMS as part of that process because it is effective in other areas. This creates clearly defined roles and responsibilities around energy and how we manage it within our facility.
A fundamental part of managing our energy is that we measure our usage of gas and electricity through meters installed at various locations throughout the plant. We create data trends from the energy that is being used, and review those trends to see where they are taking us. When we do this on a regular basis, it drives action and accountability. The data will tell us certain things, such as energy has gone up in an area, and we use the data to find out why it has gone up. If it is something we could have controlled, we use that information to drive the energy use down. If there is an area where we have driven energy down and we want to be able to sustain that, we look at how we did that and what it takes to make sure we keep doing it that way.
James Otto (left) and Gary Chastain (right), members of the Owens Corning Waxahachie plant energy team, regularly discuss energy trends with plant leader Glenn Haley (center).
Q: What are Owens Corning’s energy improvement goals?
A: Owens Corning has set a long-term goal of reducing our energy intensity by 25 percent over 10 years. This is also in line with the U.S. Department of Energy’s Save Energy Now goal.
Q: How important is energy efficiency to Owens Corning?
A: Owens Corning is all about energy efficiency. The company’s three key tenants of sustainability are greening our products, greening our operations and advancing energy efficiency in the built environment. The bottom line is that insulation saves energy and it is good sense and good business to be energy efficient in our operations on a daily basis.
Q: How does energy relate to quality, lean and safety programs at your plant?
A: Using data to track energy usage helps us to understand and reduce variability within our process. When our processes become more stable, the numbers of upsets are reduced, which helps us enhance safety, reduce quality complaints and improve our cost structure. The opportunity to identify and fix energy savings is also included in our continuous improvement events. We run kaizen events on a regular basis; and as part of those events, we challenge our teams to find energy-saving opportunities, so we get more and more people involved that way.
Q: How has this affected your plant’s implementation efforts?
A: There have really been no negative impacts to our implementation efforts at all. This has married very well with our daily operations and the direction we feel we need to go in the long term.
Q: What initially motivated your plant to apply to the Superior Energy Performance Texas pilot project?
A: When we first heard about the Texas pilot project, we felt that this program could be for energy what the Occupational Safety and Health Administration (OSHA) Voluntary Protection Program (VPP) is for safety. We really wanted to be part of developing the standards and programs that can help us and others be more energy efficient. We can see how different manufacturers can work together to help each other, like VPP does for safety. In that case, if you call the staff at another plant with questions about safety and they are a VPP plant, the doors are open and people are willing to help you, even if it is a totally different industry and manufacturer. We see how this could be done for energy efficiency and it excited us. It sounds like it would be good for everybody to be involved.
Q: What changes have you noticed in your plant’s energy program through participation in the Texas pilot program?
A: We had a good process in place to start with, but we were pretty reliant on one or two key people for a long time. This whole process has helped us to increase our documentation and has made our process a lot more robust and defined. Through this experience, we have improved our communication around data and the regular review of data. It has also driven us to broaden our base of people taking ownership and action on the energy issues that we do uncover through our normal operations. We already see a definite improvement in the amount of energy that we are using and that this level of improvement is sustainable. So, it all just makes a whole lot of sense.
Q: How will the Superior Energy Performance program and becoming an ANSI-accredited certified plant help you reach your plant’s energy goals?
A: We have reduced our energy use, so we know this is a good thing and there is certainly room to improve. The work that we have done to improve the process in the OMS is actually going to help us to sustain these gains. With operations personnel changing on an ongoing basis, the sustainability piece of this is very important to us. As far as the ANSI certification is concerned, we would like people outside of the plant to know about our plant’s commitment to being as energy efficient as possible and open the doors to help other manufacturers.
Q: If we equate the continual improvement in energy efficiency to a journey, how would you describe where your plant has been and where you would like your plant to be in the long term with regard to energy performance?
A: For us, this journey started a long time ago, and we have had some stops along the way for various reasons. Our involvement in this process has helped us to develop a much clearer road map, and we are making progress faster than we did in the past. There will always be room to improve even more as people, technology and processes change. I am not sure this is a journey that you ever complete; what is important is how far you get from the starting point.
Q: What would you tell other plant leaders about the value of implementing a management system for energy and receiving outside validation of your plant’s program and performance improvement?
A: The first thing I would say is that it is a lot of work in the beginning. We didn’t understand when we signed up for this how much work it was going to be. So, I think it is important that people understand that level of commitment. But, it is worth it. Second, measurement, data trending and regular data review are absolutely essential. You always have to understand where you are and what things need to be done. Third, you can tailor it to fit inside systems you might already be using. In our case, we incorporated our OMS into our existing ISO system. An important part of implementing an energy management system is that it creates a structure within our operation and a process that is sustainable. Again, as people turn over or equipment changes, that sustainability piece is really important.
During this process, there was also outside validation that took place, including audits, and this held our feet to the fire. It made sure that we were being honest with ourselves and doing the things we said that we were doing and were as good in some areas as we thought we were. All of those tests were quite good for us.
Editor’s note: The Owens Corning Waxahachie plant has volunteered to be the first site to participate in the official Superior Energy Performance audit in order to become an ANSI-accredited certified plant. This is scheduled to take place in November 2009.
Read More Energy Matters Articles on These Topics
This article was written by the U.S. Department of Energy’s Industrial Technologies Program and appeared in the Summer 2009 issue of the DOE’s Energy Matters newsletter. For more information, visit http://www1.eere.energy.gov/industry/.
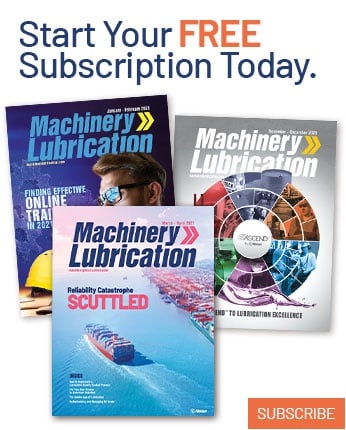