At some stage in your facilities’ life cycle, decisions were made related to what maintenance would be completed on your assets and how often it would occur. Often, these decisions are never questioned and the logic behind the decision is lost when the people that initiated them leave the business. For asset maintenance strategies to remain effective over the life of the plant, there must be an element of continuous review. In effect, your maintenance strategies must be a “living program”.
Many businesses are really good at the “Planning and Doing” in the PDCA cycle in relation to developing asset maintenance strategies, but the “Check, Act” part of the cycle is often neglected. What do you need to do to have a living program?
-
If it has been many years since anyone has effectively reviewed the asset management strategies, then start on a review process now.
-
You must engage your craftsmen/tradesmen in the asset strategy feedback process. Too often, I have seen people become frustrated because they report a work instruction is not correct. They make a point of noting it on the work order, and subsequently nothing changes. To improve the level of feedback on preventive maintenance tasks, the tradesmen and operators must see the benefit of giving the feedback. This could be benefits such as: actions that make the task less complex, actions that remove a repeat failure or actions that improve the safety of completing the task. A systematic process is required to ensure that all feedback is captured and effectively addressed. Your people need to value the work instructions, and management has to value the input from employees. If all value the process, improvements will flow.
-
Update and review of master data in your CMMS, including the equipment hierarchy, bills of materials and stock-holding levels. Do you have materials in your store that have not moved for many years and, in some cases, employees don’t know what they are for? The review and updating of master data must be considered a live process.
-
Use root cause analysis tools to determine what is causing chronic or expensive breakdowns, and then set actions to prevent recurrence. These actions must flow into a work management system and be processed through the CMMS.
-
From a cultural perspective, all maintenance supervisors must apply the lean “go and see” philosophy to strategy improvements. This is the most effective way to understand any issue, and it will also give subordinates the view that their concerns and ideas are valued.
-
Develop and document a process to assess and then manage the “flood” of improvements to documentation that will follow if the above actions are implemented effectively. Also, ensure that resources are avaliable to manage the workload.
Making your asset management strategies a living system will assist in improving machine availability, improve operational security, improve safety standards and optimize the cost of maintenance.Quantifying gains from implementing these actions is not a straightforward task, and to some extent following these recommendations is a significant “leap of faith”. However, there is enough evidence available in asset management literature that suggests that this “leap” is well worth the effort.
About the author:
Mark Brunner has a masters of maintenance management degree and a certificate in electrical engineering. He and Rod O’Connor developed The Asset Reliability Road Map. The aim is to help simplify the road to asset management excellence. For more information, contact Mark at markbrunner@thereliabilityroadmap.com or visit http://thereliabilityroadmap.com .
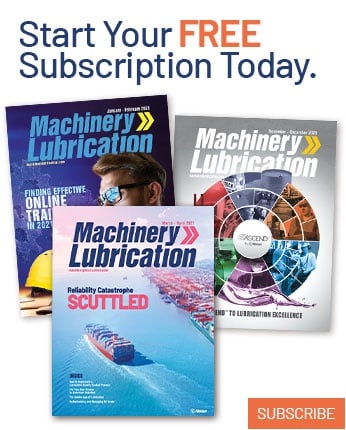