The finite element method (a.k.a. finite element analysis) originated from the need for solving complex structural analysis problems in civil and aeronautical engineering in the early 1940s.
Today, the FE method is a powerful technique used by engineers, mathematicians and scientists to solve problems in industries such as aerospace, chemical and biomechanical. The integrated finite element method and software are used to reduce the time to take products from concept to the production line.
The FE method is also used to better understand the conditions of existing structures. In a particular application on machinery vibrations, the finite element method is known as modal analysis, which allows analysts to see how a machine (or any structure) behaves under external forces or varying loads. (http://www.svibs.com/documentation/case_hct.htm)
Yet, in spite of its broad and diverse application, the FE method has never been used to eliminate manufacturing losses created by machinery breakdowns.
FE method applied to machine-based manufacturing
The underlying concept of the finite element method is very simple and can be applied to any complex structure. You can think of it as "divide to conquer". There are four basic FE steps to take for solving complex problems in manufacturing industries:
- Select the system (macro elements) to which the FE methodology will be applied.
- Develop specific subsystems (micro elements).
- Determine subsystems’ problems and solutions.
- Integrate solutions to obtain the objective (eliminate breakdown losses).
1) System selection
The FE method applies to machine-based manufacturing plants because machines are structures used for transferring and transforming power from the source to the load. The system selected for applying the FE method is “breakdown losses”. The objective for using the FE method is to eliminate the sources of all breakdown losses.
2) Developing subsystems
In order to eliminate manufacturing losses created by machinery, it is necessary to understand the sources of losses for each subsystem. The origins of breakdown losses are grouped as three micro components (subsystems):
- Breakdown Losses Created by Machines. Examples are losses created when machine components wear down.
- Breakdown Losses Created by the Manufacturing Processes. For example, a pump pumping fresh water will not have the same life expectancy as a pump pumping salt water.
- Breakdown Losses Created by People. For example, an operator or a technician creating a jam when a dropped tool gets stuck at the load side of a machine.
After finding the origin of the subsystem’s problem, a solution can be specifically developed to target each one.
This picture shows a critical gearbox (minimum of 4 hours production loss) which didn’t have a fill port or oil level gauge (later added).
3) Subsystems problems and solutions
A. Breakdown Losses Created by Machines
Problems: All machines are designed following strict standard specifications and performance parameters. Once built, machines are tested in labs under “ideal conditions” and their components’ life expectancy estimated. The environment found at most manufacturing plants is far from ideal; hence, the actual life expectancy of machinery is significantly reduced. In addition, there are other stressors, such as misalignment and unbalance, which shorten machinery life expectancy even further. It is up to the end-user to remove stressors, to maximize machinery actual life, and to determine how long a component will last in order to minimize breakdown losses.
You must consider the external stress forces which accelerate the normal wear of components, thus reducing their life even further. Unless those conditions are removed, replacing a component will not make a lasting impact. Examples of stress forces are misalignment and unbalance.
Solutions: While there are several possible solutions to address breakdown losses created by machinery, there are two processes proven to increase the actual life expectancy of machinery. These two processes are:
a) 5S for Machines (5S4M)
b) Measuring Wear and Stress (MWS)
5S FOR MACHINES
5S4M is an enhanced 5S designed to eliminate existing conditions or external stresses which affect machines. The 5S process is modified as follows:
- Seiri (Sort): Build machine’s hierarchy (plant, area, line, system, subsystem, component and subcomponent) to assess component relationships and spares availability.
- Seiton (Set/stabilize): Assign spare parts and tools within a controlled environment, making them easily and readily available (effective use of CMMS for inventory). Perform equipment modifications to enable tasks.
- Seiso (Shine): Maintain machines cleaned internally. This type of work requires experience and intricate knowledge of internal components.
- Seiketsu (Standardize): Format all maintenance processes by developing standard operating processes (SOP) and applied statistics. An example of this application is the typical maintenance emergency call. Applying the FE method lets you see which micro-component is the true source of losses. For example, you can determine if the downtime loss was longer than necessary because the parts were not available, were delivered late, or because a bad part was kept in stock. Was downtime longer because troubleshooting took too long due to lack of training? All of the above answers are seldom known. The following process diagram shows how emergency maintenance should be broken down into its micro-components to be transformed into a controllable process.
- Shitsuke (Sustain): Use software to establish a formatted communication and documentation process that ensures long-term sustainability and provides tools for analysis of breakdowns.
B) MEASURING WEAR AND STRESS (MWS)
The principal technologies used for MWS are: oil, vibration, infrared and ultrasonic analysis.
Measuring is a science used to accurately size and trend wear and stress variables using statistics and reliability growth models. Micro-elements of the Wear and Stress Measurement Process are:
The main concerns when implementing MWS are the following:
- Technology Applied: It takes around three to four years to learn all of the technologies if you already have analytical as well as hands-on machine troubleshooting experience. People responsible for MWS must have the knowledge to discern between real machine problems and false alarms. Consider only experienced people who will stay with the MWS process for a long time.
- Data Collection and Analysis: Analyzing machinery data is complex because each applicable technology assesses the wear process of a load-varying system at a fixed point in time. It is very important to have people who are comfortable and capable of dealing with information using extremely large databases and various instruments. The challenge an analyst faces is to turn data into profitable work actions instead of detailed and confusing reports.
B. Breakdown Losses Created by the Manufacturing Processes
Problems: Machinery breakdowns related to the manufacturing process originate from process variables such as heat, cold, humidity, type of load, by-products, contamination or residue created.
Some manufacturing processes create airborne particles. These particles find their way inside machinery components such as bearings and negatively alter the physical characteristic of the lubricant. This “buffing/sanding paper” effect increases internal bearing tolerances and thus reduces machinery life significantly. At other times, those airborne particles end up covering machinery components, such as frames or filters, creating a heat blanket or suffocating motors from much-needed cooling air.
Other manufacturing processes’ consistency changes from product to product. This may result in an increased load on a machine, causing it to overheat. This reduces component life, such as the internal coils on electrical motors or electronic components like SCRs (silicon-controlled rectifiers).
A more viscous mix will create an increased load on a machine, causing it overheat, thus reducing life of components. Examples are overloading conditions jamming a machine, contaminants from processed products finding their way into internal components, and creating excessive wear or diminishing clearances.
Solutions: While each industry has been utilizing specially modified and improved machinery specifically designed for their application, there is a known process which can be easily adapted and tailored to solve, or at least significantly reduce, the breakdown losses created by the manufacturing process itself. This process is called 5S for Production/Process (5S4P). The enhanced 5S process is modified as follows:
- Seiri (Sort): This step remains unchanged (eliminate the unnecessary).
- Seiton (Set/stabilize): This step remains unchanged (establish permanent locations for the essentials).
- Seiso (Shine): Clean machines externally, thus ensuring that airborne particles are quickly removed before they enter machinery components such as bearings, gearboxes or electrical panels.
- Seiketsu (Standardize): All operator processes related to machines and manufacturing process activities are standardized, and machinery statistics are put in place.
- Shitsuke (Sustain): Create communication and documentation of all processes and daily manufacturing events to ensure their sustainability.
C. Breakdown Losses Created by People
Problems - Solutions
While almost impossible to measure and account for, losses created by human errors may be the largest contributor to breakdown losses.
Problem:Losses due to a lack of seeing maintenance as a business unit. Maintenance produces some of the largest losses in manufacturing, yet we don’t measure them to find out how they could be minimized. We very seldom measure profits generated from reliability projects. Without this information readily available, executives will not provide any long-term support.
Solution:Measure and trend losses caused by reactive maintenance and profits gained from planning and scheduling repairs and other improvement projects so that executives can understand which activities produce the highest return.
Problem:Losses due to the lack of a strategic management process for eliminating all breakdown losses. Without a detailed strategy, managers will take each of the available tools and processes and implement them according to their own interpretation. When management changes, so does the process. This cyclic event typically results in many programs of the month, which are demoralizing.
Solution:Utilize a scientific method (a.k.a. Plan-Do-Check-Act) process for eliminating machine, process and people losses.
Problem:Losses due to lack of work orders generating process that is effective, efficient and most important, independent of historical data.
Solution:Generate work orders using a process NOT based on root cause failure analysis (RCFA) and one that considers implementation costs of tasks and their profitability.
4) Eliminating all sources of breakdown losses
Utilizing the FE methodology for grouping the losses into machines, processes and people provides the most effective solution to each loss. While this is very helpful, having many solutions will produce redundancy and inefficiencies. To compete in today’s economy, executives must implement solutions promptly to provide the most immediate economical advantage.
Finite Element Manufacturing (FEM) is defined as a mathematically based process that divides manufacturing into its macro and micro elements for applying maintenance, reliability and performance processes to eliminate losses and increase profits within a certain (relatively small) interval of time. The service which uses this process is FEM, a package that provides a comprehensive and cohesive solution using the following tools:
- Measures, trends and controls maintenance losses and reliability profits (MP&L) to provide prioritized solutions and address the largest losses. This provides the most immediate ROI that executives need to continue supporting FEM.
- A work order generator using 5S4M, 5S4P and MWS to optimize labor activities.
- Software (patent pending) to manage all macro and micro FEM processes.
The block diagram provides the graphical representation of how the macro elements of FEM are integrated to provide the synergy needed to eliminate all sources of breakdown losses.
With these processes providing the high-level MP&L information, executives can determine the source of losses, adjust the strategic plan and better allocate resources. Managers can improve processes and tools put in place to eliminate breakdown losses as they are uncovered. Engineers and senior technicians can perform accurate RCFA analysis and provide tools for training and communicating specific machine-related issues.
Integrating the work order generator with reliability technologies and a software tool makes the FEM process the lowest investment opportunity that provides the highest ROI. Profits are obtained within three months of implementation.
Conclusion
The application of the FE methodology in the manufacturing industry, combined with proven solutions, resulted in Finite Element Manufacturing. FEM is the first engineering-based strategic process that executives can use to eliminate all sources of breakdown losses.
About the author:
Sergio Rossi is an electrical engineer with Reliability and Performance for Manufacturing (RP4M). For more information, visit www.rp4m.com, e-mail info@rp4m.com or call 817-937-8205.
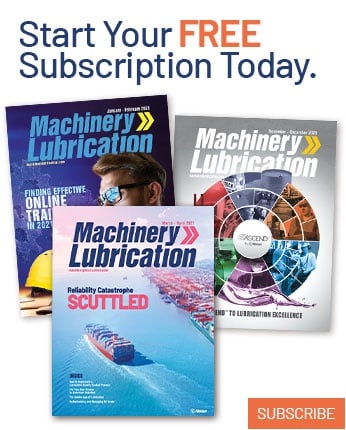