When it comes to managing operational budgets, operating and maintenance (O&M) managers face more challenges than ever in today’s economic climate. O&M budgets are constantly scrutinized to balance the cost of maintenance with replacement of aging capital equipment. The requirements of balancing reduced budgets often result in reducing the frequency of critical maintenance tasks, which cause operational inefficiencies. As funds continue to be reallocated, at times it probably seems hard to imagine making it through the fiscal year.
The energy spend to operate facilities is a significant cost that can be controlled. Effectively managing the critical components that consume electricity can result in reducing energy spend and operational costs. In most facilities, chillers are the single-largest energy-using components and can typically account for up to 50 percent of the facility’s electrical usage. Effective water treatment programs have a direct impact on chiller efficiency, saving energy and paying back big dividends. Implementing effective water treatment programs that extend the life of critical capital equipment and maximize its operational efficiency can offer businesses a competitive advantage. The following six questions will help determine whether your water treatment program is operating at peak efficiency.
Six Questions to Ask to Help Create Greater Operational Efficiencies Through Water Treatment
- What are the current operating inefficiencies in your chillers?
In many plants, the assumption is made that everything is OK if the chiller is running and the desired space is cool. However, there are factors that affect the efficient operation of the chiller(s) that can be easily overlooked and deceivingly costly. Areas of focus should include water flow rates, (in)correct temperature set points, fouled condenser tubes and cooling tower components.
- Where do the inefficiencies exist?
Heat transfer has the single biggest impact on chiller efficiency. Clean condenser tube surfaces result in the most efficient and most economical operation of the chiller. Keeping the heat transfer surfaces clean is essential to operating at peak performance and reducing maintenance costs. Effective water treatment can eliminate fouling and deposition, which will result in lower energy costs. Identifying and monitoring the critical parameters, as well as tracking daily operational points such as temperature, pressure, fluid levels and flow rates, establish historical data and ultimately identify the areas where inefficiencies exist. There are software solutions that review efficiency analysis which can lead to early indications to take corrective action if required.
- Are you measuring your utility usage?
Water usage and costs can be controlled through a uniquely designed water treatment program which can maximize cycles of concentration and reduce make-up and blowdown volumes. In some areas where water municipalities charge for sewer fees based on water delivery volumes, there is a significant amount of money paid for evaporation in systems where cooling towers are used.
Chiller efficiency tools can predict the energy consumption for individual chillers (kilowatts per ton). Significant savings can be recouped by identifying and maximizing the operation of your most efficient units. Without using these uniquely designed tools that analyze operating data points, inefficiencies not corrected over time can result in significantly higher energy costs.
- How effective is your current water treatment program?
The first priority for success in any cooling water treatment program should be to keep the system clean. Anything that interferes with heat transfer or that impacts the integrity of heat transfer makes the system less efficient and increases costs. Problems that are directly related to ineffective water treatment programs are corrosion, deposition and microbiological fouling. Consistent service that monitors and trends critical indicators of efficient performance is an essential element of a successful water treatment program. Corrective actions must be identified and implemented quickly to keep chillers running at peak efficiency. It is much easier and less costly to keep a system clean than it is to remove accumulated deposits.
- How can you troubleshoot and correct your water treatment program?
An effective water treatment program should start with analyzing the unique characteristics of the entire cooling system. A water treatment program that does not include these fundamentals goes against industry best practices and may lead to an assortment of costly problems. The elements of a successful water treatment program include consistent measurement of critical control parameters. Test results should be analyzed by experienced/qualified water treatment professionals who can determine if corrective action is needed. Visual inspections of cooling tower components (tower sumps and fill) should also be part of a routine service program. Periodic use of corrosion coupons should be part of the program assessment as well. Timely identification of system imbalances and prompt initiation of corrective actions are keys to managing a proactive water treatment program.
- How can you document “real” cost and energy savings?
The direct cost of inefficient chiller and auxiliary system operations is higher utility bills: electricity, water and sewer costs. Indirect costs of inefficient operations are increased maintenance and manpower requirements to repair the damage caused by inefficient water treatment programs.
Cost Savings and Peak Performance in any Economic Climate
The U.S. Department of Energy estimates that inefficient operation of chillers results in up to 30 percent in additional costs for electricity and water. Knowing the right questions to ask about water treatment program efficiency can clearly drive down operational costs and save valuable energy. These benefits offer a competitive advantage regardless of the economic environment, but particularly now when cutting costs is an utmost consideration for all businesses.
About the author
Fred Potthoff is co-founder of Kroff Chemical, an innovative water treatment specialist company that provides custom industrial and commercial water treatment chemicals and services to optimize plant efficiencies and reduce total cost of operation. He is an active member of the Building Owners and Managers Association, the Association for Iron and Steel Technology, and the National Association of Power Engineers. To learn more, visit www.kroff.com.
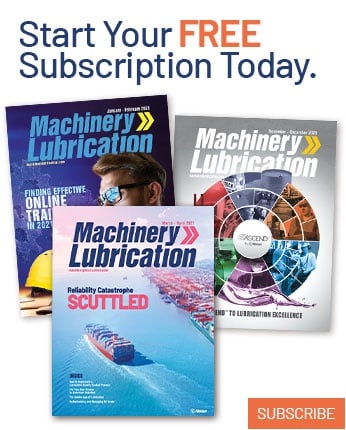