Heijunka is defined as a technique for reducing unevenness in a production cycle, which in turn reduces waste. Below, we'll discuss how to implement heijunka, its benefits and more.
What Is Heijunka?
Heijunka (pronounced hi-JUNE-kuh) is defined as a technique for reducing unevenness in a production cycle, which in turn reduces waste. It's a Japanese term that means "leveling" and is a key lean manufacturing method first used by the Toyota Production System (TPS) to develop production efficiency. Toyota realized that batching isn't sustainable and that production systems can't continuously respond to sporadic orders without suffering from uneven productivity levels, inconsistent quality, and overburdening of machines and employees, all of which results in waste.
Heijunka is often referred to as production leveling in the United States, but the two terms have the same goal: reducing unevenness in production by avoiding batching, which results in smaller inventories, lower capital costs and less overburdening of employees. Heijunka lets you produce products at a steady pace, allowing you to react to fluctuations based on your average demand. It does this in two ways: leveling by volume and leveling by type/product.
- Leveling by volume: Heijunka dictates that you should level your production by the average volume of the orders you receive. For example, if your custom apparel company gets 500 orders of gray shirts each week, but the number of shirts fluctuates by day during the week, leveling production by volume gives you the best chance to control inventory. For instance, say you receive 200 shirt orders on Monday, 100 on Tuesday, 50 on Wednesday, 50 on Thursday and 100 on Friday. Leveling demand using heijunka would require you to produce an inventory of 100 shirts every Monday. Each day after that, you would make 100 shirts a day.
-
Leveling by type/product: In reality, you probably won't be making the same exact product every day. Say your custom apparel company receives multiple types of orders for colored T-shirts each week. One week you get orders for orange (O), red (R), gray (G) and black (B) shirts. A typical mass production company would want to minimize waste that revolves around equipment changeover, so the production schedule might look like this: OOOOORRRGGBB.
However, customers frequently change their orders or volume/demand increases and decreases. What if a customer decides he actually needs the orange shirts to be gray? What if the volume of gray shirts suddenly drops, and people start ordering more black shirts? This would leave the typical mass producer scrambling to figure out how to make more gray shirts while the orange shirts just sit in inventory. To avoid this type of waste, a heijunka production schedule might look like this: OORGBOORGBOR, adding emphasis to ensure changeover times are efficient and popular items are in a buffer inventory.
Heijunka vs. Batching
Batching is popular among manufacturers because it's viewed as a cost-effective approach; there are minimal costs associated with changeover and prepared stock to meet demand. When it was first created, Ford Motor Co. was a mass producer. When the Model A was invented, Henry Ford was famous for telling the public they could have any color they wanted, as long as it was black. What was later discovered, and what Toyota found out, is that this so-called "cost-effective approach" had some pitfalls that could end up doing more harm than good. When you batch production, you more than likely will run into a few problems.
- You can't respond to customer demand. Organizations can draw up forecasts until their hands cramp, but there will always be variations and fluctuations in customer demand. Producing in batches might cost you the opportunity to give the customer what they want simply because you aren't making it at the time they want it.
- Capital is tied to inventory. Manufacturers always want to ensure they have enough product in stock to meet demand, so they produce large quantities. The problem with that is this stockpile in inventory doesn't make the company money until it is sold. You often see instances where organizations have big liquidation sales on inventory just to get rid of it, which doesn't do much for profitability.
- Overworking machines and employees. Producing large quantities constantly leads to greater chances of machine breakdowns and employee burnout. Both of these directly translate into waste, whether it's the waste of downtime or product defects/quality.
Heijunka aims to mitigate these problems by enabling companies to produce products as closely as possible to what demand requires. This is achieved by making smaller batches and creating more than one type of product at the same time. Using this approach allows organizations to roll with changes in demand while keeping inventory to a minimum.
Heijunka vs. Just in Time (JIT)
Heijunka is frequently related to or referred to in conjunction with a lean manufacturing technique known as just-in-time (JIT) production. These two concepts both try to regulate inventory. However, JIT doesn't produce the leveling seen with heijunka but instead stipulates that products be produced when they are needed in the quantity required. Heijunka aims to level the amount and types of products manufactured in a given production cycle by producing a consistent quantity of multiple products throughout a given cycle.
JIT invokes what is known as the "bullwhip effect," a phenomenon in which forecast inefficiencies lead to increasing swings in inventory when trying to respond to sporadic customer demand as you move further up the supply chain.
Heijunka and JIT have a few subtle differences, according to Honeywell's internal lean consultants, Amy Reyner and Kweku Fleming. In their Lean/Six Sigma course for MIT, they compare the two side-by-side.
Heijunka vs. JIT | |
---|---|
JIT | Heijunka |
Meets customer demand upon request | Meets customer demand in total over a period of level production |
Smaller finished goods inventory | Uses finished goods inventory to make up for short periods of higher demand |
High variability for supplier production, varying customer demand upstream | Stability for supplier, reduces inventory over the entire supply chain |
Occasional overtime | Overtime savings |
Induces the bullwhip effect | Calm upstream |
How to Implement Heijunka
Three factors affect the implementation of heijunka:
- Flexibility: Heijunka requires multiple types of products be produced in any given time frame. For example, you need to make T-shirts with three different types of logos in a 30-minute production period. This means you'll need to change out the screen-printing machine twice in that time frame. Changeover time should be done as quickly and efficiently as possible to produce all three types of T-shirts within the 30-minute time period.
- Stability: A stable production process is key for heijunka to be effective. For instance, verifying the average amount of T-shirts in each color that needs to be produced in each time frame ensures the production process remains steady. This is where knowing your takt time comes into play. Your takt time helps you create the proper production schedule so you can meet demand.
- Predictability: As mentioned earlier, while it's impossible to know the exact volume of demand, your organization should have a way to forecast customer demand. It won't always be accurate, but having a gauge on how much product is demanded by the market is better than nothing when it comes to making a production schedule.
Implementing heijunka starts with knowing your takt time and taking the following core concepts into consideration.
- Takt time is the time it takes to make a product from start to finish to meet customer demand. When implementing heijunka, it's thought of as the customer buying rate and guides the whole process. Knowing the takt time helps you determine the appropriate pace or interval for your production schedule.
- Volume leveling, as previously discussed, is when you produce based on long-term average demand and keep a buffer stock of inventory based on variability, production schedules and shipping speed.
- Type leveling is essentially visualizing production flow, making every product every day while focusing on changeover flexibility.
- Using a heijunka box is a way to visualize type leveling and your production schedule. The heijunka box will be discussed in more detail later.
- Work at a slower but more consistent pace. Think tortoise and the hare. The founder of the TPS stressed this fable in Toyota's factories, stating that being slower but consistent causes less waste and produces a more desirable product, as opposed to a hare-like mentality of being quick to get ahead and then stopping periodically to rest.
-
Focus on changeover time. Changeover time is considered the foundation on which the whole process of heijunka rests. Shortening changeover time directly improves the value stream between supply and demand. Since most manufacturers produce more than one type of product, changeover times should be as tight as possible. If your production is level, one way of doing this is by making certain your scheduled changeovers are at the same time(s) each day of the week.
Planning out changeover times this way ensures only the individuals responsible for the changeover are on the floor, so you're not paying people just to wait around.
- Buffer inventory means having a certain amount of product ready for shipment at the start of each production cycle. As mentioned in the leveling by volume example, each Monday, you would have 100 shirts ready to go. This guarantees you're leveling demand consistently and minimizing waste.
The Heijunka Box
A heijunka box is a visualization tool used for scheduling production that is leveled by type or volume. Originally a physical schedule placed on a wall, the heijunka box can either be a physical tool or a virtual tool using a software program. It's divided into a grid pattern with rectangular slots or boxes. Columns or vertical rows represent specific time periods, usually days of the week or individual shifts. Horizontal rows represent the type of product needing to be produced.
The heijunka box contains cards or "kanban" (usually color-coded) in various box slots that denote which type and in what quantity products will be produced per a specific time period. Using a heijunka box helps manufacturers implement their production sequence and evenly distribute the production of various products.
As you can see from the heijunka box illustration, each horizontal row is reserved for one type of product. Each vertical column represents identical time intervals for when a card is to be withdrawn or a product is to be produced. For example, if a shift starts at 8 a.m. and the card withdrawal interval is every 30 minutes, this means that every 30 minutes, the material handler takes the appropriate number of cards and gives them to the production process.
Each box or slot in the heijunka box signifies the timing of information flow and material. The cards in each box represent one pitch of production for one product type. Pitch is the amount of time needed to make one batch of product. Pitch can be calculated by multiplying takt time by the pack-out quantity. For example, if the takt time is 1 minute, and the pack-out quantity is 30, then 1 minute x 30 units = a pitch of 30 minutes.
In our illustration, the pitch for the orange shirts is 30 minutes, and there is one card in the box for each time interval. The pitch for the gray shirts is 15 minutes, so there are two cards in each box. The red shirts have a pitch of 60 minutes, so there is one card in every other box. Now, let's say the blue and black shirts share a production process with a pitch of 30 minutes. The demand dictates a ratio of two black shirts to every one blue shirt. This gives us one card for black shirts in the first two intervals of the shift or day and one card for blue shirts in the third shift or day, and so on.

Benefits of Heijunka
The goal of manufacturers should be to meet customer demand as smoothly and with the most predictability as possible, even though customer buying behavior is often unpredictable. Matching your production rate to customer demand as closely as possible helps create a level production process with minimal waste. Heijunka aims to do just that, providing multiple benefits along the way and targeting waste found in inventory processes.
- Surplus items: Having a warehouse full of excess inventory is one of the most frustrating problems to deal with; what do you do with products that won't be sold? This adds up to a significant cost. Heijunka strives to eliminate overproduction, which shows up on your bottom line.
- Small batches: In the same arena as surplus inventory, batching large amounts of products without considering customer demand or fluctuation can have several negative effects on an organization in addition to the cost of unsold goods. It not only can make the demand on the upstream processes erratic but also result in uneven product quality and overworked equipment and employees. All of these issues add up and can create multiple types of waste.
- Pull systems: Heijunka helps minimize waste through a pull system, which requires materials to be replaced only when they are used. Pull systems reduce costs by not purchasing materials when they aren't needed, even if the price of the material is very low and can be used to create a stockpile for later. This helps keep the waste found in transporting or stocking items to a minimum.
- Positive upstream effects: It's not uncommon for organizations to stock up on inventory in case their upstream suppliers don't deliver on time or deliver sub-quality raw materials. This leads to employees having to source the extra material and the excess inventory going unused for a long period of time. The leveling created by implementing heijunka can improve material management and ensure everything flows from the top to the bottom consistently.
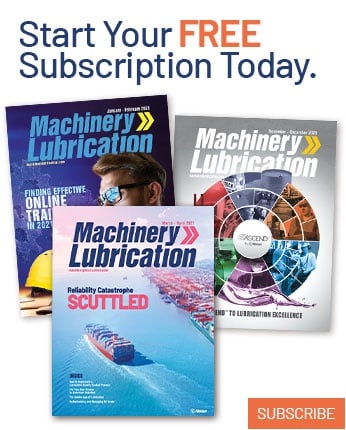