The seemingly endless search for the most elegant solutions to solve the day-to-day operating problems in manufacturing goes on and on. Today, an all-too-common mind-set is that elegant solutions mandate large investments in complex technology as the first step on the path to high performance. Unfortunately, the complexity of the elegant solution, and the diversion of resources required to implement it, can blur the real opportunities for improvement.
This blurring effect often postpones prerequisites to high-performance manufacturing when a company takes the wrong path.
Some of the most effective solutions for solving the day-to-day problems in manufacturing are well-defined and contained in an extensive body of knowledge. Amazingly, however, “across the board” application of this body of knowledge is not that commonplace. Is it because these solutions do not possess the latest of technological elegance? Maybe, but there are absolute prerequisites to the effective application of ERP and Advanced Planning systems.
Trying to build a solid structure by placing bricks in mid-air just doesn’t work. The proper foundation needs to be in place before cornerstones can be laid and the brick by brick structure is built. It is the same with software – there is no magic in software – the foundation is a prerequisite to successful use of information technology in manufacturing.
Benchmark your company
Too many manufacturers limp along without establishing the foundation that’s needed to build a high-performance manufacturing enterprise. Often times, management is so frustrated with the seeming inability to solve many of the operating problems they take a leap of faith and invest hundreds of thousands to millions of dollars in a technology solution to alleviate foundational problems in basic business processes.
Use the following 10 questions and the commentary that follows each one to conduct a self-assessment to help you “benchmark” your company’s capabilities. As fundamental as the 10 questions may appear, have your entire management team (1) answer each question; (2) meet and discuss your particular status; and, (3) outline your corrective action needs.
1) Does every product have a well-defined manufacturing and inventory deployment strategy?
Every product needs a well-defined manufacturing strategy and supporting inventory deployment plan. This is an area that needs careful attention, especially as products become more diverse and complex. For items that are engineered-to-order or made-to-order, the assumption is that an inventory deployment plan for those products is irrelevant. This is often not so. How about those raw materials and piece parts that are stocked or vendors stock in anticipation of sales for these products? Certainly, products which are made-to-stock or assembled/configured-to-order need an inventory deployment plan that fully supports the manufacturing strategy. The methodology used to develop the inventory deployment plan and the precision achieved in implementing the plan are critical to effectively executing each product’s manufacturing strategy.
2) Is your inventory record information real time and more than 99 percent accurate?
It would seem that everything must have been said on this subject and probably has.
However, inventory record inaccuracies are common problems that plague many manufacturers with resultant incalculable overhead activity costs. Acceptance of less-than-excellent inventory record accuracy will render the best systems technology useless. A well-defined and executed cycle counting program can pinpoint the root cause for errors so corrective action will be taken to permanently eliminate the cause for record inaccuracies.
3) Are bills of material 100 percent accurate?
In the literature over the years, bill of material accuracy measures of less than 100 percent were considered acceptable. This results in manufacturing having to figure out and compensate for the inaccuracies. Again, record inaccuracies create rippling chaos which can render the best of systems useless. The overhead activity costs that can be directly tied to inaccurate bills of material are enormous. Moreover, inventory levels and cycle times are increased as a result.
The only acceptable bill of material is 100 percent accurate.
4) Are the forecasting process and demand variability integrated with a service-oriented inventory and/or capacity deployment strategy?
Are you in one of those companies where some people say, “We can’t forecast this business...” and, therefore, the responsibility is passed off to someone else? Whether this is the case or not, if you maintain any inventory and/or capacity in anticipation of future orders, you are forecasting. In many companies, the wrong persons with the wrong tools are doing the forecast and deploying inventory and/or capacity in the wrong way. As a result, there is probably too much inventory, too little service, and a production operation that’s frequently driven into chaos from the demand and supply imbalance in the system.
Fortunately, there is hope for those long frustrated by the forecasting dilemma. Any business can be forecasted. The degree of effectiveness is a direct result of how well the forecasting process is developed and then supported by appropriate policies, tools, techniques and measurements.
5) Do you have a comprehensive and effective sales and operations planning (SOP) process that is management’s handle on sales, production and inventory plans?
In most manufacturing companies, SOP is not as well-defined and refined a process as it should be, if it’s really being done at all. Without an effective SOP process you are flying blind with the added danger of altitude and direction changing without warning. Developing an appropriate plan is a critical success factor for manufacturers. Nothing can be more critical in planning than:
-
What are we planning to sell?
-
What are we planning to make?
-
What is our planned result?
-
What are the actuals?
With these numbers known, top management has a handle on the numbers that drive the overall business. When adjustments are needed to keep demand and supply in balance, the SOP provides the essential decision support process. The “ultimate measures” of profit, cash flow and return on investment are largely determined from the demand and supply actuals. As such, the SOP process deserves high priority in management’s activities.
6) Do you start the assembly process without any material shortages?
In stationary assembly companies, such as machinery producers, the common mode of operation is to kit and issue to begin assembly with what parts are available and then start the mad expediting scramble to cover the shortages. The lack of an appropriately sequenced flow of material to assembly causes assembly time to be 150 to 200 percent or more of what it should take and is a significant overhead activity cost. When a company decides to implement demand-based flow manufacturing, it has essentially mandated “zero shortages” will be the operating mode.
In a properly designed demand-based flow manufacturing system, each succeeding step of the process is designed to be linked and dependent on the previous process step. When a production system is designed to have material flow without any interruption, then any and all problems causing material flow imbalance or stoppage must be permanently solved or nothing works. To many, the approach of “everything works or nothing works” is so counter to conventional thinking it may seem so radical that it’s viewed as impossible or labeled “it will never work here; we’re different.”
Achieving high-velocity material flow in manufacturing may take some time to achieve but the process to get there will solve so many seemingly unsolvable problems that many very tangible benefits will accumulate. As a result, the payoff can be very high and fast; long before excellent flow is actually achieved.
7) Do you have a comprehensive and dynamic inventory performance monitoring system that pinpoints problems of likely inventory excesses before they occur?
Excess inventory is really the result of the poor business processes that cause the inventory to exist in the first place. Pinpointing and prioritizing the actions a planner should take to prevent excess inventory from accumulating is something that MRP systems do not perform very well. True, MRP will advise what deferrals are needed, but without a prioritized dollar impact on inventory excesses, the planner is at a disadvantage as to what the sequence of deferrals should be.
If you’re thinking that the deferrals are taken care of in the normal daily routine of a planner – the answer could be yes, but more likely it’s maybe or no. The fact of the matter is planners know that management places a higher priority on avoiding shortages, rather than excesses which causes planners to place and expedite orders long before deferring orders if there’s any time left. The requirement in decision support must be to identify those few deferral actions that will have the most impact on avoiding the accumulation of excess inventory.
8) Has the impact on service and inventory from cycle time reduction been properly analyzed and quantified?
Queues of information and or material are the single biggest reasons for long cycle times in most plants. Conventional practices and push systems are the primary causes for queues to exist and for cycle times to often be more than twice what they could be. With lots of work-in-process in the way, it is virtually impossible to create and maintain a prioritized flow of material through production.
Demand-based flow manufacturing should be the longer-term goal. However, in the near term, manufacturing can realize some significant cycle time reduction by reducing queues through controlling input and output. Be prepared however, to take on the various “rejection rebellions” that will take place as the traditional mindset will reject the queue limit logic.
Preparatory education can be very helpful, but until reduced queue time is in practice for a few months, widespread acceptance will be minimal until everyone realizes it is a better way to work.
9) Have all supply chain processes been analyzed to clearly identify value added and non-value-added activities, bottlenecks, queues, cycle times, etc.?
If you are serious about your pursuit of world-class manufacturing performance, then process analysis is a prerequisite to developing your new procedures. I recommend that most manufacturers start with the process mapping of the order-to-delivery cycle. This is more than likely the most complex of your processes and also the area of greatest opportunity.
The order-to-delivery cycle always begins with the information flow that proceeds and actually activates material flow. All the way through the order-to-delivery process, it is very important that non-value-added activities, constraints, queues and cycle times be identified and quantified. Once you know where you are, you can start the most exciting process of defining “where we could be.”
10) Have you specifically defined the barriers that prevent you from achieving world-class manufacturing performance?
There are numerous possible barriers which are unlikely to appear on a process map that prevent even starting on the road to world-class manufacturing. For example, how people are measured may reward behavior that is counter to your goal. In the worst case, if the barrier is senior management, then the organization will have to wait until the understanding and/or pain level gets high enough for the CEO to lead the effort.
Unfortunately, too few companies can answer all 10 questions with a “yes.” Answering all the questions affirmatively does not mean your company is World Class, but it will mean you have started on a good path. Applying ample doses of commonsense, good business practice may not seem elegant, but it is a springboard to becoming a high-performance manufacturer.
About the author:
R. Michael Donovan is the president of R. Michael Donovan & Co. Inc., an international management consulting firm. Contact him at 508-788-1100 or mdonovaninc@msn.com. The firm’s Web address is www.rmdonovan.com.
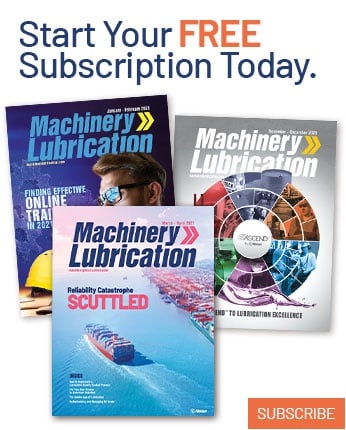