The Shingo Prize was established in 1988 to promote an awareness of lean manufacturing concepts and to recognize companies that achieve world-class status. The Shingo Business Prize has been dubbed by Business Week the “Nobel Prize of Manufacturing.” The Shingo Research Prize recognizes and promotes research and writing regarding new knowledge and understanding of manufacturing consistent with the philosophy and criteria of the Shingo Prize for Excellence in Manufacturing.
The Shingo Prize program is administered by the College of Business at Utah State University. Ross Robson is the program's executive director. Robson will be one of the featured speakers at "Lubed, Reliable and Lean," Noria Corporation's international conference and exhibition May 16-18 in Columbus, Ohio. For more information on this world-class conference, visit www.driveyourplant.com.
Among the Shingo research award winners, the first book, Kaikaku: The Power and Magic of Lean by Norman Bodek, provides an introspective look at the evolution and transformation of lean practices and books from Japan that catapulted Productivity Inc. and Productivity Press to a prominent status in the North American manufacturing community. Based on antidotal details of meeting some of the manufacturing geniuses of our time, Bodek captures in clear detail many of the principles and techniques of what we know of today as Lean Manufacturing. For first time as well as seasoned readers and practitioners of Lean Manufacturing, the book provides an insightful review of the foundation of both continuous improvement and radical change.
A second book, The Toyota Way by Jeffrey K. Liker, explains Toyota’s unique approach to lean and its 14 management principles and philosophy that drive Toyota’s quality and efficiency-obsessed culture. The book provides valuable insights that can be applied to any organization and any business process, whether in services or manufacturing. It is full of examples of the 14 fundamental principles at work in the Toyota culture, and how these principles create a culture of continuous learning and improvement. You’ll discover how the right combination of long-term philosophy, process, people, and problem solving can transform your organization into a lean, learning enterprise – the Toyota Way.
The third book, Who’s Counting? A Lean Accounting and Manufacturing Business Novel by Jerrold M. Solomon, is a business novel that explains how manufacturing and accounting must develop a partnership to successfully achieve world-class results. It exposes the financial surprises that will surface during a successful lean journey and provides a road map to bring accounting practices into the 21st Century. The book illustrates how all the usual objections of the accounting department can be overcome, including compliance with both Internal Revenue Service guidelines and Generally Accepted Accounting Practices. The book covers the difficult topic of lean accounting in an easy to read format that appeals to all of the functional areas involved in a lean transformation.
The first applied publication, Creating Level Pull by Art Smalley, shows readers how to advance a lean transformation from a focus on isolated improvements to improving the entire plant-wide production system by implementing a lean production control system. This workbook is unique because it is a step-by-step case study on how to implement a level, pull-based production control system, which is a new step toward “system kaizen” that is not yet well understood outside of Toyota. Using a realistic example facility, the author shows readers how to make the transition to a robust pull system and answers a series of 12 critical questions, including what items to hold in finished goods inventory and what items to make to order, how to buffer the system against instability, how to schedule batch processes, and how to level the production schedule.
The second applied publication, Making Materials Flow by Rick Harris, Chris Harris, and Earl Wilson, is a workbook that shows manufacturing professionals in operations, production control, and industrial engineering how to replace material-handling systems designed for mass production with systems that support lean production. The workbook uses plain language and illustrations to explain how to create, sustain, and improve a lean material-handling system for purchased parts. The authors break down the implementation process for readers by leading them through ten simple pragmatic questions that show how to apply the relevant concepts and methods in a step-by-step progression. The workbook also contains the formula, standards, and forms needed to implement the system.
The last applied publication, The Complete Lean Enterprise – Value Stream Mapping for Administrative and Office Processes by Beau Keyte, offers a step-by-step approach to applying lean initiatives to the administrative and office environment. It is a read for leaders looking to improve their production support activities within their order-to-cash value stream. The workbook is a valuable tool in applying value stream mapping to non-production areas, identifying office wastes, establishing performance metrics, speeding up administrative workflow, and improving office efficiency.
The first article, “Learning to Lead at Toyota” by Steven J. Spear, describes the experiences of a new hire to Toyota named Bob Dallis, an outstandingly successful manager at his previous employer, also an automaker. Unlike a traditional transition for someone of Dallis’s stature, he experiences a Karate Kid like training spending weeks in hands-on problem solving on the shop floor. As a result, Dallis discovers much about the managerial processes that Toyota uses to facilitate continuous improvement across a broad range of functions by a broad range of measures. Dallis comes to see his senior manager’s role in an entirely different light. He realizes that his job is to facilitate a cascade of problem-solving-related training and skill development that allows people at all levels to make meaningful contributions to bettering the work that they do.
A second article is “Managing Learning Curves in Factories by Creating and Transferring Knowledge” by Michael A. Lapre and Luk N. Van Wassenhove. Through an analysis of quality improvement projects conducted in one factory over a decade, this article identifies two dimensions of the learning process: 1) conceptual learning, which yields know-why, and 2) operational learning, which yields know-how. However, replication of this production line in other factories within the same firm fell short of expectations; neither creation nor transfer of such knowledge occurred. The evidence shows that a stable environment with continuity in resources, such as raw materials suppliers, enhances knowledge creation. Moreover, successful replication requires management buy-in and knowledge diversity.
The third article, “High Performance Product Development: A Systems Approach to a Lean Product Development Process” by James M. Morgan, compares and contrasts Toyota’s product development system to that of a North American competitor through an in-depth analysis of the automotive body development process in an attempt to understand how Toyota is able to consistently outperform their competitors in product development speed and quality. The article examines what, if any, is the link between Toyota’s product development process and the effectiveness of the Toyota Production System. This study identifies the underlying principles that form the core of the powerful systems approach to product development used by Toyota in which the fundamental system elements of process, people, and tools and technology are found to be mutually supportive and coherent in nature.
The last article is “The Effects of Just-in-Time/Lean Production on Worker Job Stress” by Robert Conti, Jannis Angelis, Cary Cooper, Brian Faragher, and Colin Gill, is the first known large-scale, multi-industry empirical study of the relationship of job stress to a range of lean practices, as well as to the degree of lean implementation. The results are based on 1,391 worker responses from 21 manufacturing sites in four UK-industry sectors. Eleven work practices are found to be significantly related to job stress, and an unexpected non-linear response of stress to lean production implementation is identified. The results and their implications are discussed in the article.
Further information regarding these works and the Shingo Prize can be found at www.shingoprize.org.
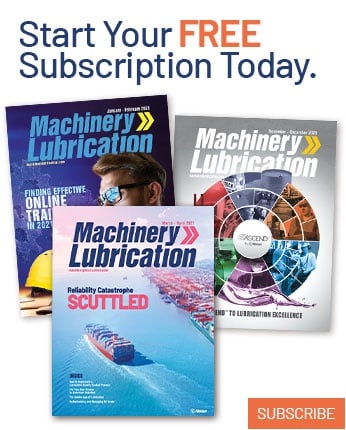