In 1999, FUJIFILM Manufacturing USA Inc. began a 130,000-square-foot distribution center expansion project at its site in Greenwood, S.C. The project was dictated by an anticipated 50 percent increase in material handling volume. The challenge was to increase the handling volume without increasing the site’s operational staff. After an in-depth study of the process, FUJIFILM investigated the use of automated guided vehicles (AGVs). The availability of an AGV that could perform in a very narrow aisle application turned out to be the ultimate solution.
The automated system designed by the facility includes four narrow aisle turret trucks, provided by AGV Products Inc. of Charlotte, N.C., and in-bound and out-bound accumulation conveyors for each aisle.
About FUJIFILM
FUJIFILM USA Inc., is a U.S. subsidiary of FUJIFILM Corporation of Tokyo, Japan. It provides digital and analog photographic imaging systems, recording/storage media and motion picture film products and services to consumers, professionals and businesses. The company was established in the U.S. in 1965 and is headquartered in Valhalla, N.Y., with offices and distribution centers throughout the country.
FUJIFILM brings continuous innovation and leading-edge products to a broad spectrum of industries including medical, life sciences, consumer electronic, chemical, graphic arts, information systems, photography and office products based on its vast portfolio of digital, optical, fine chemical and thin film coating technologies. The company provides products and services that contribute to the advancement of culture, science, technology and industry, as well as to improved health and environmental protection. It is the global leader in digital mini-labs; computed radiography systems; ink dyes, pigments and UV inks for inkjet printers and materials used in the production of flat panel displays. It was ranked No. 18 for U.S. patents granted in 2005, employs more than 75,000 people worldwide and in the year ended March 31, 2006, had global revenues of $22.8 billion.
About its Greenwood facility
FUJIFILM Manufacturing USA Inc., began manufacturing operations at the 500-acre Greenwood, S.C., campus in 1988, when the company announced the construction of its first U.S. factory for the production of pre-sensitized plates for the graphic arts market. The manufacturing complex is currently comprised of five high-tech manufacturing plants, the Greenwood Research Laboratories, and the largest FUJIFILM distribution center in the world. The 1,200 associates employed in Greenwood manufacture digital and conventional pre-sensitized plates, color photographic paper, QuickSnap one-time-use recyclable cameras, and digital and conventional medical imaging products.
The approximately 500,000-square-foot distribution center (DC) consists of three main areas: raw materials, partial picking operations and full pallet operations. Products produced at each of the seven manufacturing plants on campus are delivered to the DC and stored for delivery to regional distribution centers.
“The Greenwood facility is a strategic production hub in the FUJIFILM family of companies around the world,” says Keith Butler, distribution center manager for FUJIFILM Manufacturing USA. “Over the past few years, we have added the production of several digital products that required additional storage capacity and increased our material handling needs. In addition to conventional imaging and information products, we now manufacture digital photographic paper, digital printing plates and digital dry medical imaging film.”
AGVs solve throughput dilemma
Butler states that the increased volume dictated a more cost-efficient method of handling inbound and outbound loads.
“We added approximately 130,000 square feet to the DC, but we didn’t want to add operating staff,” he says. “We investigated other material handling methods and finalized on the AGVs. The full pallet storage area has the highest number of moves, so we chose to implement the AGV system there. Prior to the use of AGVs, we were utilizing Man-up VNA turret trucks in the rack area. Additional pallet moves required additional vehicles, and AGVs eliminated the need for more drivers.
“In the dock area, we still transport pallets and load trucks with conventional sit-down forklifts and pallet jacks. The other areas of the DC utilize a variety of vehicles including sit-down forklifts, stand-up forklifts, order pickers, side loaders and VNA trucks.
“As we learn to use the system more efficiently, we anticipate additional benefits, including higher productivity, eliminating non-value-added activities, continuous operation (no breaks, etc.), less handling of products, reducing potential damage and more coordination when picking and storing pallets.
“The system was designed so that the AGVs could service all aisles in the warehouse. An ASRS fixed-aisle concept would have required a crane for each aisle. The AGV solution is ideal for our application. We had relatively rigid parameters – i.e. low ceilings, existing racks, etc. – requiring the AGV system to be adaptable. Our storage racks are seven levels high, with 30 pallet positions on each side of a very narrow aisle. Each storage location houses a pallet and the system has a capacity of 12,000 pallets.”
“The biggest challenge during the installation was timing. Unfortunately, implementation started during our peak shipping season and it required products to be removed from the racks and then reloaded utilizing the AGVs. With the large volume of products we were moving, this became very difficult and resulted in a great deal of overtime. However, everyone worked together and made this project a success in spite of the challenges.”
AGV details
The FUJIFILM application is one of AGV Products’ first installations of “the automated warehouse”. The Automated Warehouse System offers a variety of benefits such as continuous operation, reduced plant damage, improved logistics and safety, advanced material tracking and reduced labor requirements. Typical applications can be found in a variety of facilities, such as warehouse and distribution centers, manufacturing plants, beverage and food processing plants, third-party logistics providers and e-commerce companies.
Warehouses benefit from the marriage of automated guided vehicle technology and conventional industrial trucks. The system combines a modified (VNA) very narrow aisle truck manufactured by Hyster Company and AGV Products’ guidance controls and software, as directed by their TRACE (Traffic Routing AGV Command Executor) system controller. The driverless operation is capable of complete “lights out” operation from the warehouse receiving area to the shipping dock. Best of all, the vehicles can be introduced into current operations, using the existing racking and floor.
Automated turret trucks are introduced into the automated warehouse, allowing users to maximize floor space and storage density. Rack aisle widths can be set as close as 18 inches wider than the widest load to be handled, and in almost every situation, the facility’s existing racking is used. The trucks handle loads up to 4,000 pounds at a maximum extended height of 24 feet. They are equipped with a hydraulic rack and pinion turret that is capable of rotating 180 degrees, allowing the truck to access both sides of the aisle without turning around. Once automated, these vehicles continue to retain their manual operational features, which can be reactivated with the turn of a key switch.
The Automated Warehouse System utilizes AGV Products’ advanced TRACE AGV System Control Software that interfaces with the existing warehouse management system to coordinate movement of all vehicles within the warehouse. TRACE runs the Windows 2000 operating system on a Pentium PC and features inventory control as well as a variety of networking options. The heart of the system’s user interface is a graphics package that displays the vehicle’s position, load, and stationary equipment status and movement, in real time.
AGV Products is a leading designer and manufacturer of automated guided vehicle systems, vehicle control software, and other factory and warehouse material handling automation. Automated products and services include: turnkey AGV systems with standard and custom-built vehicles; software and control packages for AGVs, and AGV system retrofits.
For more information on automated guided vehicles, call 704-845-1110 or visit www.agvp.com.
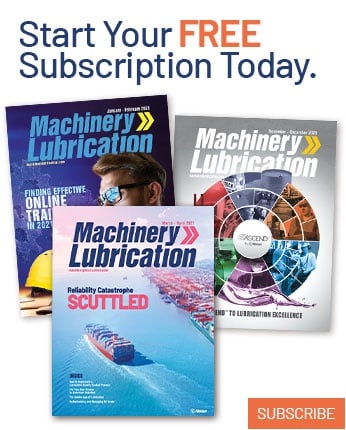