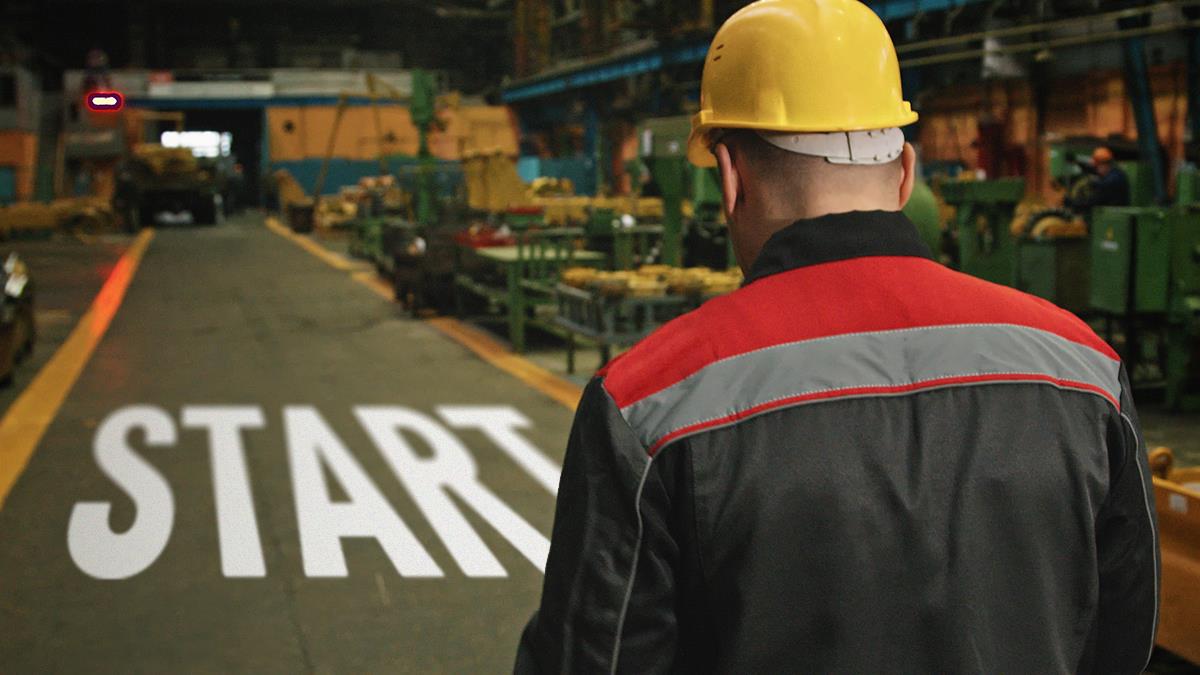
Every reliability and maintenance professional, leader, and change agent may have a natural inclination to initiate the implementation of best practices right away — simply taking action. In essence, they embrace the "just do it" approach to business management.
Some individuals might choose to kickstart the process by enhancing planning and scheduling practices, while others may immediately delve into training for best practices in lubrication or shaft alignment. While these approaches can yield results, it's worth considering if there is a more established sequence of steps to follow for the best starting point.
Throughout my career, I've been responsible for instigating cultural changes in reliability and maintenance across three different plants and have also served as a consultant for more than 40 global locations. Over the past 36 years, I've gathered a wealth of experiences, including both successes and failures, along with valuable lessons. In my retirement, my objective is to assist others in applying these lessons to enhance the efficiency of their plants.
Where and When the Journey Must Begin
"When should you commence your reliability journey? As the Chinese proverb wisely states, 'The best time to plant a tree was 20 years ago; the second-best time is now.' Let's face the reality — in the realm of maintenance, there's never an ideal moment. Waiting until tomorrow, next week, next month, or even next year won't necessarily yield better outcomes unless you actively shape the future through effective leadership, knowledge acquisition, and meticulous planning. It's essential to understand that hope alone won't suffice as a strategy.
Consider how many years you may have put off implementing best practices, often due to factors like new business ventures, market share loss, cost-cutting measures, workforce shortages, financial constraints, and even unforeseen events like the COVID-19 pandemic. Many hesitate to prioritize reliability as a key driver of business success because they buy into the misconception that it demands substantial upfront investments and promises delayed returns. However, this notion is inaccurate, provided you know this crucial insight: Each reliability and maintenance best practice is specifically crafted to eliminate inefficiencies within your facility. By strategically applying the most appropriate practices to address the unique sources of waste within your plant, you can achieve swift, enduring, and scalable improvements.
The crucial step that often eludes most individuals is determining the actual sources of waste in their plant, which encompass issues, inefficiencies, rising costs, and machine downtime. It's a critical error in deployment to deduce your plant's wastage solely from Key Performance Indicators (KPIs) and management opinions — I emphasize that this mistake can have severe consequences. The only reliable method to identify wastage is through a technique known as "Chalk Circle Observation," a process originally outlined by Toyota's Taiichi Ohno.
To execute this process, individuals need to spend a substantial amount of time on the shop floor, typically a minimum of eight hours (though 3-10 days is not unusual). These participants should prepare to be astonished by the chasm between the KPIs, their subjective assessments, and the stark reality they encounter during these observations. Armed with this intimate understanding, my experience in guiding such interventions has consistently unveiled numerous solutions, many of which are cost-effective or require minimal expenditure and can be implemented within a matter of days, if not hours.
Here are some examples of actions resulting from this process:
-
Implementing comprehensive job kitting with audits for all planned work.
-
Establishing a site lube specialist to provide training in precision lubrication practices.
-
Initiating tracking and auditing of preventative maintenance compliance.
-
Conducting a Preventive Maintenance (PM) review to ensure that failure modes are effectively addressed with actions.
-
Requiring feedback and improvement suggestions for all completed work orders. These actions lead to swift, sustainable, and scalable results — a guarantee that it can be this straightforward.
With this understanding of the power of observation, the question arises: Is this the right starting point? Yes, and the "who" involved should be your plant's leadership team. This transformation is fundamentally about changing the organizational culture, not merely deploying tools. The everyday decisions made by leadership will either bolster or hinder this change. Alignment is crucial; all stakeholders must buy into the notion that reliability is a top priority.
For instance, the production department must commit to outage times, resource allocation, and operating equipment within design parameters. Safety management should view planned work and process stability as key elements in preventing injury risks. The Human Relations manager should connect reliability best practices with employee satisfaction and retention. The controller must recognize the impact on plant capacity and costs.
"The crucial step that often eludes most individuals is determining the actual sources of waste in their plant, which encompass issues, inefficiencies, rising costs, and machine downtime. It's a critical error in deployment to deduce your plant's wastage solely from Key Performance Indicators (KPIs) and management opinions — I emphasize that this mistake can have severe consequences. The only reliable method to identify wastage is through a technique known as "Chalk Circle Observation," a process originally outlined by Toyota's Taiichi Ohno."
The Kaizen Process
Here's my proposed approach for aligning the leadership team, which I refer to as a "Kaizen" — a Japanese business philosophy emphasizing continuous improvement in work practices and efficiency:
-
Introduction of Reliability Best Practices (2 hours on Monday): Initiate by introducing common reliability best practices and emphasize how they address the various sources of waste within a plant. For example, discuss how planning and scheduling can enhance crew safety, efficiency, precision, and reduce both planned and unplanned downtime. This initial step should be led by a change agent, reliability leader, plant manager, or a consultant.
-
Observation Teams (Tuesday, Wednesday, Thursday): On Tuesday morning, assign leaders to two-person observation teams. These leaders will learn best through shared experiences, so it's ideal to have at least three teams. Each team should be assigned a full 8-hour day of observations. While eight hours may seem lengthy, it is essential to allow sufficient time for waste to surface, which it inevitably will.
The observations can encompass tasks like preventive maintenance, planned repairs, following unplanned work crews, or monitoring the operation of a production center. These tasks should be selected based on KPIs and the leadership team's opinions, which provide insights into waste areas. The teams should report to their designated observation tasks 10 minutes before the start of the shift and take detailed notes. Importantly, the observers should refrain from intervening in the tasks they are observing.
After the 8-hour observation, each team should convene in a conference room to summarize their findings and share them with the other teams. This session should be facilitated and kept concise, lasting no more than 60 minutes. After the report-out, each team receives their observation assignments for the next two days (Wednesday and Thursday).
Three days of observations are typically sufficient to gain a comprehensive understanding of the existing wastes in the plant. Be prepared to hear expressions like "This is the worst day I've ever seen at our plant" after day one and day two's report-outs. It's only after the third day that the leadership team will fully grasp the reality of the wastes in the plant. It's essential not to shortcut this process, as it could lead to dismissing the observations as anomalies.
-
Consolidation of Observations (Friday morning, 90 minutes): Gather the leadership team in a conference room and collectively analyze the observations to identify common themes. These themes might include, for instance, waiting on parts, improper equipment usage by operators, operational failures in equipment turnover, and crews rushed to the point of being unable to perform precision work. Connect these identified waste areas with appropriate best practices.
-
Zero to Low-Cost Solutions (90 minutes): From the list of waste areas and best practices, work as a group to formulate 10-20 zero to low-cost solutions that can be put into action within the next 30 days. Focus on quick, simple wins that everyone will notice. Assign action owners, and establish schedules for follow-up and progress reporting.
-
Establish an Ongoing Process (Reliability Lead Team): Create a structured process for ongoing additions of actions, review of status, assistance needed by action owners, and tracking KPIs. This could be organized as a "Reliability Lead Team" to maintain the momentum of continuous improvement.
The Kaizen process achieves success by instigating a profound emotional impact on leaders. Witnessing waste firsthand over a challenging 3-day period is significantly more potent than merely relying on Key Performance Indicators (KPIs). This experience should generate enduring leadership support, transcending business cycles. Once you've set the reliability flywheel in motion with consistent sponsorship and achieved rapid results, leaders become more inclined to invest due to the newfound credibility.
For instance, this could involve initiatives such as establishing a dedicated lubrication room, providing training, making equipment modifications, and obtaining certifications in condition monitoring technologies.
Moreover, it's crucial to establish a comprehensive marketing and communication strategy — a step that should not be overlooked. I strongly recommend a monthly report summarizing the actions taken, the results achieved, and any challenges faced. It's essential for leaders to connect the dots between actions and outcomes.
Examples of this could include:
-
"Within 60 days, we improved lubrication PM completion from 50% to 95%, resulting in a reduction of machine downtime from 12% to 6% in just 6 months."
-
"We eliminated 1000 hours of PMs that weren't addressing failure modes, reducing the backlog from 16 weeks to 9."
Furthermore, I advise sending out two success story emails per week, ideally with visuals and brief descriptions. For instance, sharing a success story like identifying and repairing a faulty electrical connection within 30 minutes, preventing a repeat of a catastrophic failure that caused 24 hours of unplanned downtime in 2015. These marketing practices serve as a safeguard for your reliability best practice journey when faced with cost-cutting pressures. Your results will underscore reliability as a "waste elimination machine," and your efforts should be accelerated, not delayed.
“Go forth and do great things.”
— Tom Moriarty
Cultural transformation need not be a source of fear. The role of the change agent is to create new experiences that reshape beliefs. These newly formed beliefs, in turn, lead to changed actions and ultimately, improved results. Sustaining this journey over time is crucial for achieving remarkable outcomes. Therefore, it is advisable to commence with your lead team.